Best Technology Guide to Ultrasonic Flow Meters.
Ultrasonic flow meters are non-intrusive type liquid flow meters. Ultrasonic flowmeter measures the flow by detecting the effect of fluid flow on an ultrasonic beam (or ultrasonic pulse). There are two types of ultrasonic flow meter technologies: Doppler shift and transit-time.
Ultrasonic flowmeters measure the fluid flow rate in a pipe. With the sound waves transit time principle to determine the flow rate. Ultrasonic flow meters, with easy installation, could be clamp on, handheld, and portable.
Ultrasonic meters are ideal for liquid applications. Like: water, wastewater, Fuel, applications or any dirty liquid in the pipe. And for Natural Gas flow measurement, SI-3404 Ultrasonic Gas Flow Meteris a new type flow meter.
Featured Ultrasonic Flow Meters
- What is an Ultrasonic Flow Meter?
- Features of Ultrasonic Flow Meters
- Aadvantages and Disadvantages of Ultrasonic Flow Meter
- Types of Ultrasonic Flow Meters
- Ultrasonic Flow Meters Specifications
- How Ultrasonic Flowmeters Work
- What is non-intrusive ultrasonic flow meter technology?
- How to Use Ultrasonic Flowmeters
- Industries Where Used
- Application Cautions for Ultrasonic Flowmeters
- How to install an ultrasonic flow meter?
- How to select a clamp on ultrasonic flow meter?
- Q&A
- Technical Support
What is an Ultrasonic Flow Meter?
Ultrasonic flow meters are non-intrusive devices that use acoustic vibrations to measure the flow rate of liquid. There are two types, Doppler and transit time.
Ultrasonic meters are ideal for wastewater or any dirty liquid which is conductive or water based. But will generally not work with distilled water or drinking water. These flow meters are also ideal for applications where low pressure drop, chemical compatibility, and low maintenance are required.
The external clamp type or tube type ultrasonic flow meter is based on the principle of “speed difference method. Ultrasonic flowmeter measures the liquid flow in the round tube. It uses advanced multi-pulse technology, digital signal processing technology and error correction technology to make the flow meter more suitable for the industrial environment. More convenient, economical and accurate measurement.
In 1842, Christian Doppler discovered that: A stationary observer perceives a sound to have shorter wavelengths as its source approaches. Longer wavelengths as its source recedes.
The Doppler effect explains why one hears rising pitch in the blowing horn of an approaching car. When the car zooms away, the pitch seems to drop. Ultrasonic Doppler flow meters put this frequency shift to work in so-called dirty liquids containing acoustical discontinuities; suspended particles, entrained gas bubbles or turbulence vortexes.
Know more about Ultrasonic flow meter – Wikipedia
Features of Ultrasonic Flow Meters
Ultrasonic flowmeter is a non-contact instrument that has been applied with the rapid development of integrated circuit technology in the past ten years. It is suitable for measuring fluids that are not easy to contact and observe, as well as large pipe flow.
- Simple structure, easy to install and use.
- Energy saving. No additional resistance is generated and no pressure loss.
- Suitable for difficult to measure media and large pipelines.
- Simple structure, convenient installation, use and maintenance.
- Easy to maintain. The inspection parts are easy to repair and replace, and do not need to be cut off (except for the built-in type).
- The unique signal digital processing technology makes the instrument’s measurement signal more stable, strong anti-interference ability and more accurate measurement.
- Non-mechanical transmission parts are not easily damaged, maintenance-free, and long life.
- The circuit is more optimized and highly integrated; low power consumption and high reliability.
- Intelligent standard signal output. Friendly man-machine interface, multiple secondary signal outputs for your choice.
- Pipe section type small diameter measurement is economical and convenient. And the measurement accuracy is high.
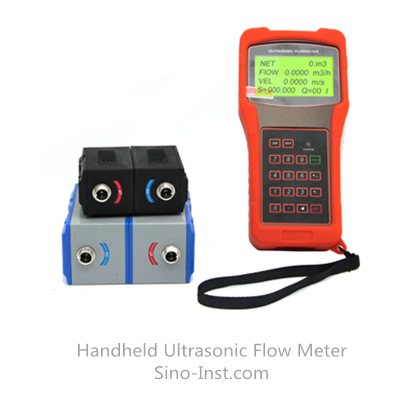
Aadvantages and Disadvantages of Ultrasonic Flow Meter
Advantages
- This technology can be very accurate and is used for custody transfer (meaning accounting accurately for an expensive fluid) of natural gas and petroleum liquids.
- There is no pressure loss. A type that can perform detection from the outside of piping is available.
- Ultrasonic flowmeters are available in sizes to 72 inches and larger.
- High turndown (can read low as a percentage of the full scale or top reading), handles high pressures, is repeatable (consistent), handles extreme temperatures, can be used clamped to the outside of a pipe without penetration, is low maintenance, highly reliable and self –diagnosing.
- Ultrasonic flowmeters do not obstruct flow so they can be applied to sanitary, corrosive and abrasive liquids.
- Some ultrasonic flowmeters use clamp-on transducers that can be mounted external to the pipe and do not have any wetted parts.
- Temporary flow measurements can be made using portable ultrasonic flowmeters with clamp-on transducers.
- Clamp-on transducers are especially useful when piping cannot be disturbed, such as in power and nuclear industry applications.
- In addition, clamp-on transducers can be used to measure flow without regard to materials of construction, corrosion, and abrasion issues.
Disadvantages
- A long section of straight pipe is required.
- Liquids that have a large solid content will cause malfunctions.
- Measurement is not possible when there are many air bubbles.
- High cost.
- Sensitivity to stray process vibrations, problems with pipe diameter change due to buildup and clamp-on units have lower accuracy.
- The use of clamp-on transducers introduces additional ultrasonic interfaces that can affect the reliability and performance of these flowmeters.
- In particular, if not properly applied and maintained, attenuation of the ultrasonic signal can occur at the interfaces between the clamp-on transducers and the outside pipe walls, and between the inside pipe walls and the fluid.
Types of Ultrasonic Flow Meters
- Plug-in ultrasonic flowmeter: can be installed and maintained without stopping production. The ceramic sensor is used for non-stop installation using a special drilling device. Generally, it is mono measurement. To improve the measurement accuracy, three channels can be selected.
- Pipe segment type ultrasonic flowmeter: need to cut the pipeline to install, but the future maintenance can be stopped. Choice of mono or tri-channel sensors.
- External clamp-on type ultrasonic flowmeter: can perform fixed and mobile measurement. Use special coupling agent (silicone rubber cured at room temperature or high-temperature long-chain polymer grease) for installation, and the pipeline will not be damaged during installation.
- Portable ultrasonic flowmeter: portable use, built-in rechargeable lithium battery, suitable for mobile measurement, with magnetic sensor.
1. Non-contact measurement method, small size, easy to carry
2.Suitable for on-site measurement of sound conducting media of pipes of various sizes
3.The built-in Ni-MH rechargeable battery can work for more than 20 hours
4. Flexible user interface and easy to use
5. Intelligent on-site printing function to ensure the integrity of traffic data
6. Equipped with an integrated aluminum alloy protective box, which can be used in harsh outdoor environments - Hand-held ultrasonic flowmeter: small size, light weight, built-in rechargeable lithium battery, handheld use, equipped with magnetic sensors.
- Explosion-proof ultrasonic flowmeter: It is used for the measurement of liquid flow in explosive environments. That is, the converter is explosion-proof and the sensor is intrinsically safe.
Ultrasonic Flow Meters Specifications
Items | Performance & Parameter | |
Transmitter | Data Interface | Insulate RS232 serial interface, upgrade the flowmeter software by computer |
Special Cable | Twisted-pair cable, under 50 m; RS485, transmission distance can over 1000m | |
Pipe Installation Condition | Material | Steel, Stainless steel, Cast iron, Copper, Cement pipe, PVC, Aluminum etc. |
Diameter | 32~6000mm | |
Measuring Medium | Liquid type | Such as Water (hot water, chilled water, sea water, waste water, etc.); Oil (crude oil, lubricating oil, diesel fuel oil etc.) etc. |
Temp. | -30~160℃ | |
Turbidity | No more than 10000ppm and less bubble | |
Flow rate | 0~±10m/s | |
Working Environment | Temp. | Transmitter:-20~60℃; Flow Transducer:-30~ 160℃ |
Humidity | Transmitter: 85%RH; Flow Transducer:IP67 | |
Power Supply | 3 AAA built-in Ni-MH batteries 1.2V(operation for over 12 h); 90V-260VAC adapter | |
Power Consumption | 1.5W | |
Dimension | 200*93*32mm (transmitter) |
Items | Performance & Parameter | |
Convertor | Principle | Transit- time ultrasonic flowmeter |
Accuracy | ±1% | |
Display | 2×20 character LCD with backlight, support the language of Chinese, English and Italy | |
Signal Output | 1 way 4-20mA output,electric resistance 0~1K,accuracy 0.1% | |
1 way OCT pulse output (Pulse width 6~1000ms,the default value is 200ms) | ||
1 way relay output | ||
Signal Input | 3 way 4-20mA input,accAuracy 0.1%,acquire signals such as temperature,press and liquid level | |
Achieve to heat maesurement by connecting the temperature transducer PT100 | ||
Data Interface | Insulate RS485 serial interface,upgrade the flowmeter software by computer,support MODBUS | |
Data Record | Thermal printer,external SD card (2G of capacity) | |
Pipe Installation Condition | Pipe Material | Steel, Stainless steel, Cast iron, Copper, Cement pipe, PVC, Aluminum, Glass steel product, liner is allowed |
Pipe Diameter | 15~ 6000mm | |
Straight Pipe | Transducer installation should be satisfied: upstream10D, downstream 5D, 30D from the pump | |
Measuring Medium | Type of Liquid | Single liquid can transmit sound wave,such as Water (hot water, chilled water, city water, sea water, waste water, etc.); Sewage with small particle content; Oil (crude oil, lubricating oil, diesel oil, fuel oil, etc.);Chemicals (alcohol, etc. ) ; Plant effluent; Beverage; Ultra-pure liquids, etc. |
Temperature | -30~160°C | |
Turbidity | Less than 10000ppm and less bubble | |
Flowrate | 0~±10m/s | |
Working Environment | Temperature | Convertor:-20~60C; Flow Transducer:-30~ 160C |
Humidity | Convertor: 85%RH; Flow Transducer:IP67 | |
Power Supply | 8 built-in Ni-MH batteries 1.2V(for over 20 hours of operation).90V-260VAC adapter | |
Power Consumption | 1.5W |
Items | Performance & Parameter | ||
Host | Principle | Transit- time ultrasonic flowmeter | |
Accuracy | ±1% | ||
Display | 2X20 character LCD with backlight, support the language of Chinese, English and Italy | ||
Signal Output | 1 way 4~20mA output, electric resistance 0~ 1K, accuracy 0. 1%(optional);1 way OCT pulse output(Pulse width 6~1000ms, default is 200ms); 1 way Relay output | ||
Signal Input | 3 way 4~20mA input, accuracy 0. 1%, acquisition signal such as temperature, press and liquid level; Connect the temperature transducer Pt100, can finish the heat/energy measurement | ||
Data Interface | Insulate Rs485 serial interface, upgrade the flowmeter software by computer, support the MODBUS | ||
Special Cable | Twisted-pair cable, generally, the length under 50 meters ; Select the RS485, transmission distance can over 1000m | ||
Pipe Installation Condition | Pipe Material | Steel, Stainless steel, Cast iron, Copper, Cement pipe, PVC, Aluminum, Glass steel product, liner is allowed | |
Pipe Diameter | DN32~6000mm | ||
Straight Pipe | Transducer installation should be satisfied: upstream10D, downstream 5D, 30D from the pump | ||
Measuring Medium | Medium | water,sea water ,alcohol,Acid and alkali,waste water,beer,all kinds of oil Single liquid can transmit sound wave. | |
Temperature | -30~160℃ | ||
Turbidity | No more than 10000ppm and less bubble | ||
Flowrate | 0~±7m/s,Forward and backward measurement | ||
Work environment | Protection grade | Host:IP67;flow sensor:IP68 | |
temperature | Host:-20~60℃;flow sensor:-30~ 160℃ | ||
Humidity | Host: 85%RH; Flow sensor:can measure under water, water depth^2m (tansducer sealed glue) | ||
Power Supply | DC8~36V or AC85~264V | ||
Power Consumption | 1.5W | ||
Dimension | 132*150*85mm(host) |
Item | PUA Gas Ultrasonic Flow Meter |
Accuracy | 1.4% , Repeatability: 0.4% 1.0% , Repeatability: 0.2% |
Diameter (MM) | DN25-DN300 |
Input signal | Flow signal: 200 KHz±10% Temperature signal: analog signal output by temperature sensor |
Output | Pulse / RS485 |
Press | 1.6Mpa, 2.5MPa, 4.0MPa, 16MPa, 40MPa |
Power | 24VDC or 3.6V Lithium battery |
Power consumption | Internal power supply: average power consumption ≤1.5mW, two lithium batteries can be used continuously for more than 6 years. External power supply: average power consumption ≤1W |
Connection | Flange |
How Ultrasonic Flowmeters Work

Principles
When the ultrasonic beam propagates in a liquid, the flow of the liquid will cause a small change in the propagation time. And the change in the propagation time is proportional to the flow velocity of the liquid. The relationship is as follows:
Which
θ is the angle between the sound beam and the direction of liquid flow.
M is the number of linear propagations of the sound beam in the liquid.
D is the inner diameter of the pipe.
Tup is the propagation time of the sound beam in the positive direction.
Tdown is the propagation time of the sound beam in the reverse direction.
ΔT = Tup –Tdown
Let the speed of sound in a stationary fluid be c. The velocity of the fluid flow be u. And the propagation distance be L.
When the sound wave is in the same direction as the fluid flow (that is, in the downstream direction), its propagation velocity is c + u.
Otherwise, the propagation velocity is cu .
Place two sets of ultrasonic generators and receivers (T1, R1) and (T2, R2) at two places separated by L.
When T1 transmits ultrasonic waves in the forward direction and T2 in the reverse direction.
The time required for the ultrasonic waves to reach the receivers R1 and R2 is t1 and t2, then:
t1 = L / (c + u); t2 = L / (c-u)
Because in industrial pipelines, the velocity of the fluid is much smaller than the speed of sound, that is, c >> u, the time difference between the two is ▽ t = t2-t1 = 2Lu / cc.
It can be seen that when the sound wave propagates in the fluid c When known, the flow velocity u can be obtained by measuring the time difference ▽ t, and the flow rate Q can be obtained.
The method of flow measurement using this principle is called the time difference method. In addition, phase difference method and frequency difference method can be used.
What is non-intrusive ultrasonic flow meter technology?
The non-intrusive detection method means that the detection medium will not cause wear to the detection instrument, so there will be no leakage.
In the flow detection of liquid media, the clamp-type ultrasonic flowmeter made by the ultrasonic detection method that has been used for a long time. And has become a standard flow detection product. In the field of chemical product production, especially in the measurement of corrosive media or media harmful to human health. People are most willing to use this non-immersive ultrasonic testing method. But these advantages are not limited to instruments for liquid detection.
In recent years, ultrasonic flow detection technology has been increasingly used for the detection of gaseous media. Especially in the process of natural gas transportation, transportation and storage, non-immersive detection methods have also been widely used. In the process gas detection, this non-immersive ultrasonic clamping detection technology is very beneficial.
We specialise in measuring the flow of a liquid in a pipe by using clamp on /strap on sensors. These are high frequency sensors that penetrate through the pipe wall and the liquid to determine the fluid velocity, flow rate and total. The most common types of clamp on technologies use a doppler or transit time propagation technique.
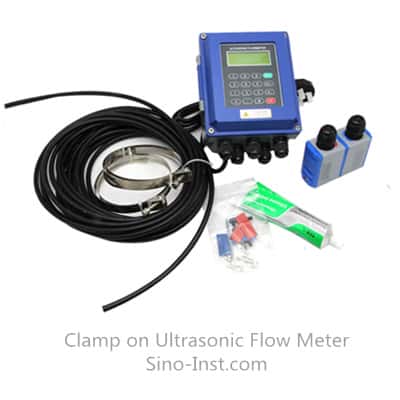
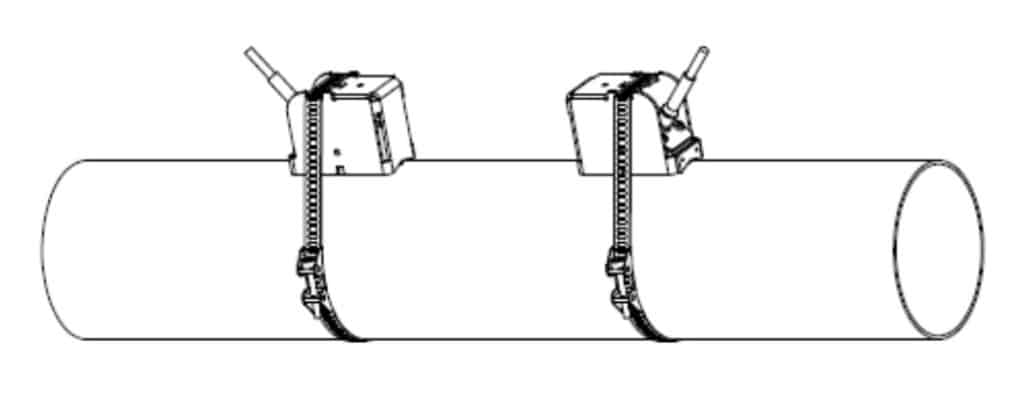
How to Use Ultrasonic Flowmeters
- Ultrasonic flowmeters are commonly applied to measure the velocity of liquids that allow ultrasonic waves to pass. Such as water, molten sulfur, cryogenic liquids, and chemicals. Transit time designs are also available to measure gas and vapor flow.
- Be careful because fluids that do not pass ultrasonic energy. Such as many types of slurry, limit the penetration of ultrasonic waves into the fluid.
- In Doppler ultrasonic flowmeters, opaque fluids can limit ultrasonic wave penetration too near the pipe wall, which can degrade accuracy and/or cause the flowmeter to fail to measure.
- Transit time ultrasonic flowmeters can fail to operate when an opaque fluid weakens the ultrasonic wave to such an extent that the wave does not reach the receiver.
Industries Where Used
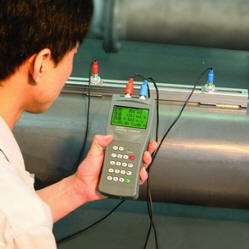
The industries in order of higher to lower are:
Oil and gas; Water and wastewater;
Power; Chemical; Food and beverage;
Pharmaceutical; Metals and mining; and pulp and paper.
Application Cautions for Ultrasonic Flowmeters
- The flowmeter has two modes of diagonal and reflection. When the reflection mode cannot be measured, the diagonal mode may be able to measure, so that we have always used the reflection mode.
- The flowmeter has high requirements on the pipeline, and the insulation layer must be scraped off, otherwise it cannot be measured.
- When we measure the air-conditioning water system, use a knife to cut off the insulation layer to prevent the sensor, and then stick the cut insulation layer after the measurement. The surface of the pipe is as bright as possible. If it is too rough, it must be polished with sandpaper.
- It is difficult to measure when the fluid in the pipeline is not full, so the measurement location should be as straight as possible, away from elbows, valves and other places.
- The authenticity of the flowmeter reading depends on the signal strength. When the signal is too low, the result is basically unreliable, and generally it is more than 60% or even more.
- Since the readings may vary greatly, the approach we take is to allow the flowmeter to take continuous readings, such as continuously reading for one minute and then taking the average.
- Measuring hot water lines is more difficult than cold water lines. Because the temperature of the hot-water pipe wall surface is high, the couplant is easily made at high temperatures. In addition to the product’s own couplant, we have all tried toothpaste.
- For transit time ultrasonic flowmeters, be sure that the fluid can adequately conduct ultrasonic waves. Because the flowmeter will not measure when the ultrasonic waves cannot penetrate the flow stream between the transducers.
- Ultrasonic waves must be able to penetrate the fluid for Doppler flowmeters to operate accurately.
- When the fluid is relatively opaque and does not penetrate the fluid, Doppler flowmeters tend to measure the velocity of the fluid at or near the pipe wall, which can cause significant measurement error and/or cause the flowmeter to fail.
- For Doppler ultrasonic flowmeters, be sure that the fluid adequately reflects ultrasonic waves. Because the flowmeter will not operate without a reflected ultrasonic signal.
- Depending upon design, reflections can occur due to small bubbles of gas in the flow stream or the presence of eddies in the flow stream. If not already present in the flowing stream, generating these sources of reflection can be difficult in practice. Fortunately, some combination of bubbles of gas and/or eddies are present in most applications.
- The velocity of the solid particles in slurry can be different than its liquid carrier fluid. Be careful applying ultrasonic technology when the solid particles can become concentrated in one part of the flowing stream. Such as in a horizontal pipe flowing at a relatively low velocity.
- Be careful when applying Doppler ultrasonic flowmeters in slurry applications. Because the solid particles can produce strong signals that can cause the Doppler flowmeter to measure the velocity of the solids and not the velocity of the liquid.
- Avoid fluids that can coat wetted transducers or coat the pipe wall in front of non-wetted transducers. Because the flowmeter will not measure when the ultrasonic waves cannot enter the flow stream.
- Be sure to maintain reliable clamp-on transducer connections to the pipe wall. Because the flowmeter will not measure when the ultrasonic waves are not able to reach the fluid.
- Be sure to understand the process and apply these flowmeters properly. For example, a periodic cleaning process upstream may cause the flowmeter to stop working because the dirt may not allow ultrasonic energy to pass through the fluid.
- Further, if the dirt coats wetted transducers, the flowmeter may fail to operate until it is cleaned.
How to install an ultrasonic flow meter?
The transit-time ultrasonic flowmeter is a competitive flow measurement method in the world today. And its measurement line accuracy is higher than 1.0%. Due to the diversity of the industrial site, especially the environment around the pipeline, how to install and debug the ultrasonic flowmeter according to the specific environment has become an important subject in the field of ultrasonic flow measurement. This regulation details the installation details of the ultrasonic flowmeter. It further fully reflects the advantages of accuracy, reliability and stability of the ultrasonic flowmeter, greatly reducing future maintenance work and even maintenance-free.
Detailed installation
The ultrasonic flowmeter should be aware of the situation before installation, including:
- What is the distance from the host where the sensor is installed;
- Pipe material, pipe wall thickness and pipe diameter;
- Pipeline age
- Fluid type, whether it contains impurities, bubbles, and whether it is full;
- Fluid temperature
- Whether there are interference sources at the installation site (such as frequency conversion, strong magnetic fields, etc.);
- Four season temperature at the place where the host is placed;
- Whether the power supply voltage used is stable;
- Whether remote signals and types are needed;
According to the on-site conditions provided above, manufacturers can configure the on-site conditions, and can also make special models if necessary.
Installation location
The selection of the installation pipe section has a great impact on the test accuracy. The selected pipe section should avoid the two situations that have a large impact on the measurement accuracy.
Generally, the selection of the pipe section should meet the following conditions:
- Avoid installing machines in pumps, high-power radio stations, frequency conversion, that is, where there is a strong magnetic field and vibration interference;
- Select pipe sections that are uniform and dense and easy for ultrasonic transmission;
- To have a long enough straight pipe section, the upstream straight pipe section of the installation point must be greater than 10D (Note: D = diameter), and the downstream must be greater than 5D;
- the installation point upstream from the pump should be 30D distance;
- The fluid should fill the pipeline;
- There should be enough space around the pipeline for on-site personnel to operate. Underground pipelines need to be tested wells.
Installation method
Ultrasonic flowmeters generally have two probe installation methods, namely Z method and V method.
However, when D <200mm and the site conditions are one of the following conditions, the Z method can also be installed:
- When the turbidity of the fluid to be measured is high, no signal is received or the signal is weak when measured by the V method;
- When the inner wall of the pipeline is lined;
- When the service life of the pipeline is too long and the inner wall has serious fouling;
For those with better pipeline conditions, even if D is slightly larger than 200mm, in order to improve the measurement accuracy, V method can be used for installation.
Probe position
- Enter the parameters of the pipeline into the instrument and select the probe installation method to obtain the installation distance;
- On horizontal pipelines, generally choose the middle of the pipeline, avoiding the top and bottom (the top may contain air bubbles and the bottom may have sediment);
- V method installation: first determine a point and measure another point at a horizontal position according to the installation distance.
Z method installation: first determine a point, measure another point at a horizontal position according to the installation distance, and then measure the symmetrical point of this point on the other side of the pipeline.
Pipeline processing
After determining the position of the probe, within the range of ± 100mm between the two installation points, use an angle grinder, file, sandpaper and other tools to grind the pipe to a bright and smooth pit.
Requirements: uniform gloss, no undulations, smooth and round feel. Special attention should be paid to the fact that the grinding point must have the same arc as the original pipe. Do not sand the mounting point to a flat surface, and wipe this area with alcohol or gasoline to facilitate probe bonding.
Wiring
Probe and instrument wiring
Probe (sensor)
The probe can be divided into three types according to the actual measurement pipeline:
S-type sensor (15 ~ 100mm)
M-type sensor (50 ~ 700mm)
L-type sensor (300 ~ 6000mm)
Fine-tune the probe
After connecting the wires, fill the inside of the probe with silicone. Leave it for half an hour. Then fix the probe to the polished pipe with silicone and clamps (note the direction of the probe, the lead end is outward). Then observe the signal strength Ratio to transmission time. If it is found to be bad, finely adjust the probe position until the signal of the instrument reaches the specified range
How to select a clamp on ultrasonic flow meter?
Before ordering, the following questions must be considered. With answers to the following questions we can select the appropriate flow device and ship it to your location.
What are the pipe sizes of the liquids that are going to be measured?
What is the minimum and maximum process temperature of the application?
Do you require a portable battery operated unit or a permanent fixed flow monitor powered by mains?
What are the output requirements? E.g. analog, digital, pulse?
What is the minimum and maximum flow rate for the flow meter?
What is the minimum and maximum flow velocity?
Is there a length of straight pipe away from bends and pipe disturbances?
Is the pipe always filled with liquid?
Q&A
The transit time ultrasonic flowmeter uses the time difference method to measure the flow rate. That is, the sound wave of a certain speed changes its propagation time between two receivers (or transmitters) due to the fluid flow. This relative change can be obtained by measuring this relative change. The flow velocity of the fluid, and then calculate the flow rate by parameters such as flow velocity.
When the ultrasonic flowmeter measures the flow, the ultrasonic transducer can be placed outside the pipeline without direct contact with the fluid, without damaging the flow field of the fluid, and without pressure loss. It can be used for flow measurement of various liquids. Includes flow measurement for corrosive liquids, high viscosity liquids and non-conductive liquids. It is especially suitable for measuring the water flow of large-caliber pipes or the speed and flow of various canals, rivers and seawater. It is also used in medicine to measure blood flow.
(1) The transit time method is applied to clean, single-phase liquids and gases. Typical applications are factory discharge fluid, weird fluid, liquefied natural gas, etc .
(2) Good experience in gas application in the field of high pressure natural gas;
(3) The Doppler method is suitable for two-phase fluids with a low heterogeneous content, such as: untreated sewage, factory discharge fluid, dirty process fluid; it is generally not suitable for very clean liquids.
Ultrasonic waves will be scattered if they encounter tiny solid particles or bubbles in the propagation path. Because the time difference method does not work well when measuring fluids containing such things. It can only be used to measure relatively clean fluids.
The Doppler method works by using the characteristic that ultrasonic waves are scattered. So, the Doppler method is suitable for measuring fluids containing solid particles or bubbles.
But, because scattering particles or bubbles exist randomly, the sound transmission properties of fluids are also different.
If the fluid with poor sound transmission performance is measured, the scattering is strong in the low velocity region near the wall of the tube.
While the fluid with good sound transmission performance is dominant in the high velocity region, which makes the Doppler measurement accuracy low.
Although the transmitting transducer is separated from the receiving transducer. So that only the scattering in the middle region of the flow velocity section can be received, the measurement accuracy is still lower compared with the time difference method.
Positive displacement flow meter also called Volumetric flow meter.
Volumetric flow measurement uses a fixed small volume to repeatedly measure the volume of fluid passing through the flowmeter. Therefore, there must be a space forming a standard volume inside the volumetric flowmeter, which is usually called the “metering space” or “metering room” of the volumetric flowmeter. This space is composed of the inner wall of the meter case and the rotating parts of the flow meter.
The working principle of a positive displacement flow meter is that when a fluid passes through the flow meter, a certain pressure difference will occur between the inlet and the outlet of the flow meter. The rotating part (rotor for short) of the flow meter rotates under this pressure difference and discharges the fluid from the inlet to the outlet. In this process, the fluid fills the “metering space” of the flow meter again and again, and then is continuously sent to the outlet. For a given flow meter, the volume of the measurement space is determined, as long as the number of rotations of the rotor is measured. The cumulative value of the volume of fluid passing through the flowmeter can be obtained.
Volumetric flowmeters are classified according to their measuring elements and can be divided into elliptical gear flowmeters, scraper flowmeters, double rotor flowmeters, rotary piston flowmeters, reciprocating piston flowmeters, disc flowmeters, and liquid-sealed barrel flowmeters , Wet gas meter and membrane gas meter.
Technical Support
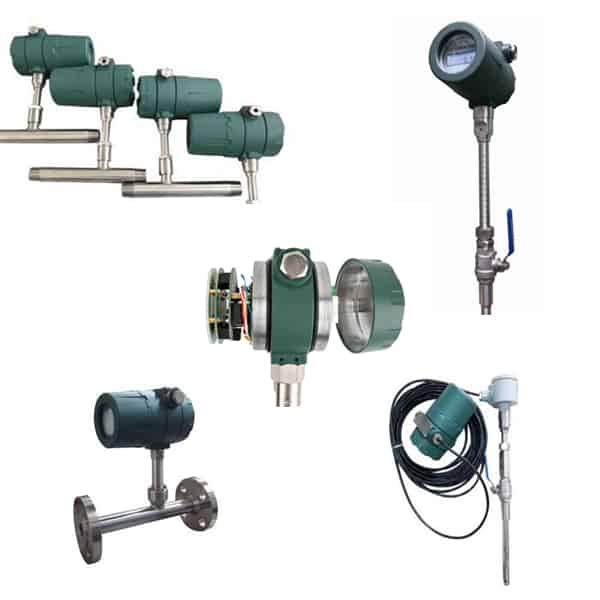
Thermal Mass Flow Meter Technology
Thermal Mass Flow Meter (TMF) also called Thermal Flow Meter. Thermal Mass Flow Meters measure the mass flow of a fluid. An external heat source will heat the pipe or the fluid. Temperature field changes when the fluid flows through the pipe. Thermal mass flow meter measures the relationship between the energy required to increase the temperature of a fluid and the mass of the fluid to measure the mass flow of the fluid. The flowmeters directly measure the mass flow or normalized volume flow of gases. Without any additional pressure and temperature compensation. Generally, thermal mass flow meter used to measure the mass flow of a gas (like natural gas).
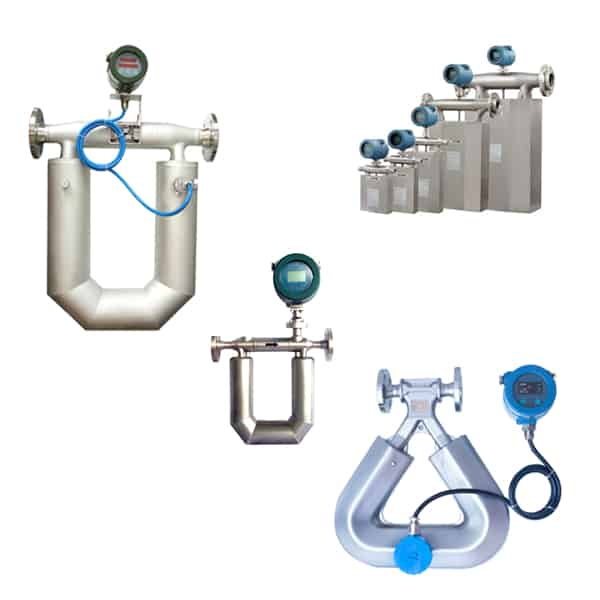
Coriolis Mass Flow Meter Technology
Coriolis mass flow meter also called micro motion flow meter. Coriolis mass flow meter is the mass flow meter beasd on the coriolis force. Coriolis mass flow meter and thermal mass flow meter are the most common mass flow meters. Corolis mass flow meters are best choice for all process and custody transfer (CT) applications. Coriolis mass flow meter can measure different values at the same time. Mass, volume flow, density and concentration measurement of liquids and gases. This is the most important difference among Coriolis mass flow meter, DP and oval gear flow meters.
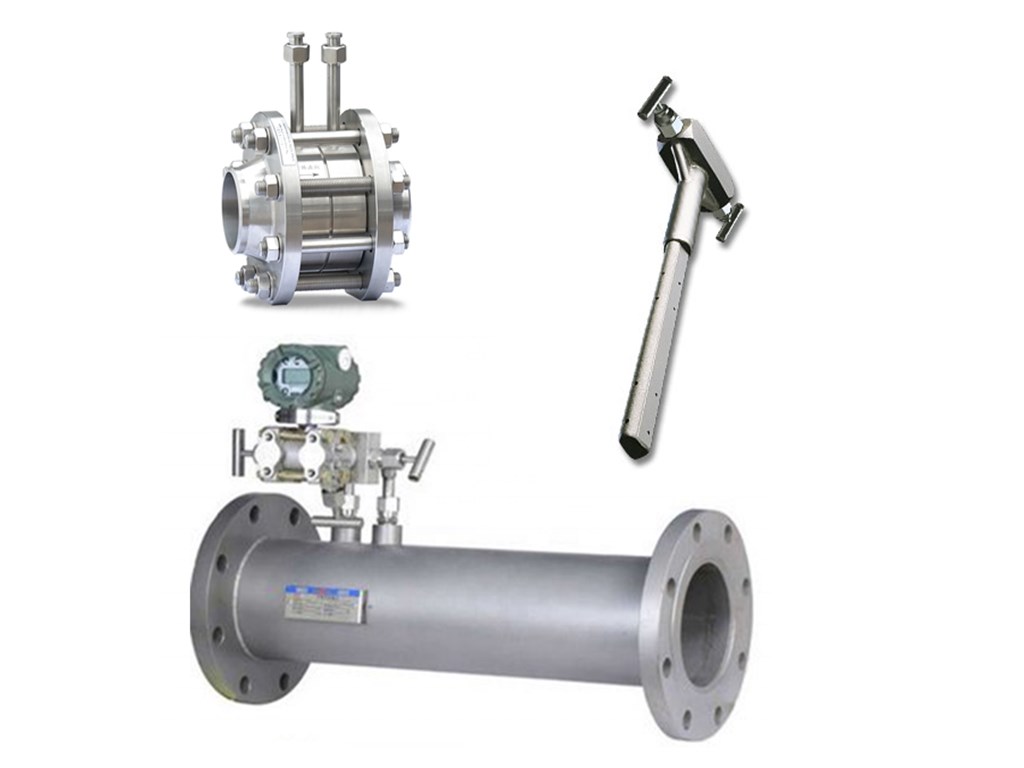
Differential Pressure Flow Meter Technology
Differential Pressure Flow Meters also called DP flow meters. Differential pressure flow meters consist of flow sensors and pressure/differential transmitters. DP Flow Meters measure the flow rate based on the differential pressure measured by the flow sensor parts. Flow sensors are the important part of differential pressure flow meters. Like: Orifice plate, Venturi tube, Wedge, V-cone and Averaging Pitot Tubes. Differential pressure (DP) flow meters are suitable for applicaitons, like: water, gas, steam, oil….
Sino-Inst is a Professional ultrasonic flowmeter manufacturer and supplier from China. Sino-Inst offers over 10 ultrasonic flow meter products.
A wide variety of ultrasonic flow meter options are available to you, such as free samples, paid samples.
Sino-Inst’s ultrasonic flow meters service for industrial applications. Like: Cooling water, industrial gas, corrosives and brine, chemical processing, mining. Wastewater, energy, electronics, laboratories, medical, and many other industries.