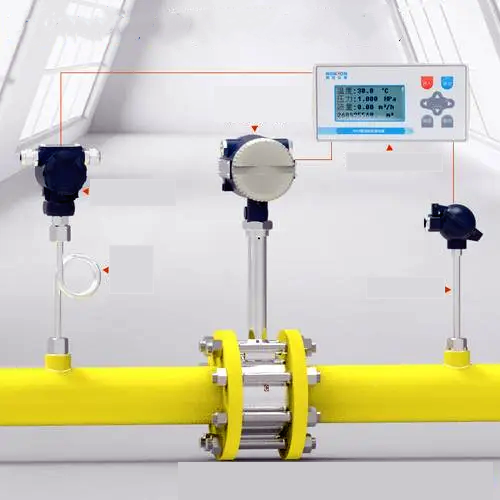
The principle of temperature compensation and pressure compensation of the flow meter is based on the changes in physical parameters such as density and viscosity of the fluid at different temperatures and pressures, which affects the measurement accuracy of the flow meter. In order to eliminate this effect, temperature and pressure compensation is required.
When we purchase a flow meter, we often encounter temperature compensation and pressure compensation configurations, especially for measuring gases, steam, etc. Next, let’s analyze in detail what is the temperature compensation and pressure compensation of a flow meter?
What is pressure compensation?
Pressure compensation is mainly a way to correct the large changes in the quality of the medium under different pressures when detecting flow.
If the flow meter detects volume flow, what is needed is mass flow, volume flow * density = mass flow. Density is a constant under temperature and pressure, but the density of this medium has a relatively small effect on temperature and can be ignored. However, if the pressure of this medium changes slightly, the density will change greatly. Therefore, it is necessary to detect the pressure to calculate the density of the medium, which means pressure compensation is required.
What is temperature compensation?
Temperature compensation is an adjustment method whose purpose is to make the reference temperature of the free end of the sensor more suitable.
In sensor applications, the sensor itself and the measured substance usually have certain temperature coefficients. Will change its own parameters as the ambient temperature changes. A series of technical measures taken to prevent the sensor’s indicators and performance from being affected by temperature changes are called temperature compensation technology.
For example, in flow measurement, there is a square root relationship or a proportional relationship between the flow rate and density of the fluid. However, the density of many fluids, especially gases, changes with changing operating conditions. Therefore, the density of the fluid needs to be compensated for temperature and pressure.
Of course, in addition to flow meters, there are other measuring instruments that also use temperature compensation. For example: PH detector, water quality analyzer, frequency meter, ultrasonic level meter, temperature sensor, pressure transmitter, etc.
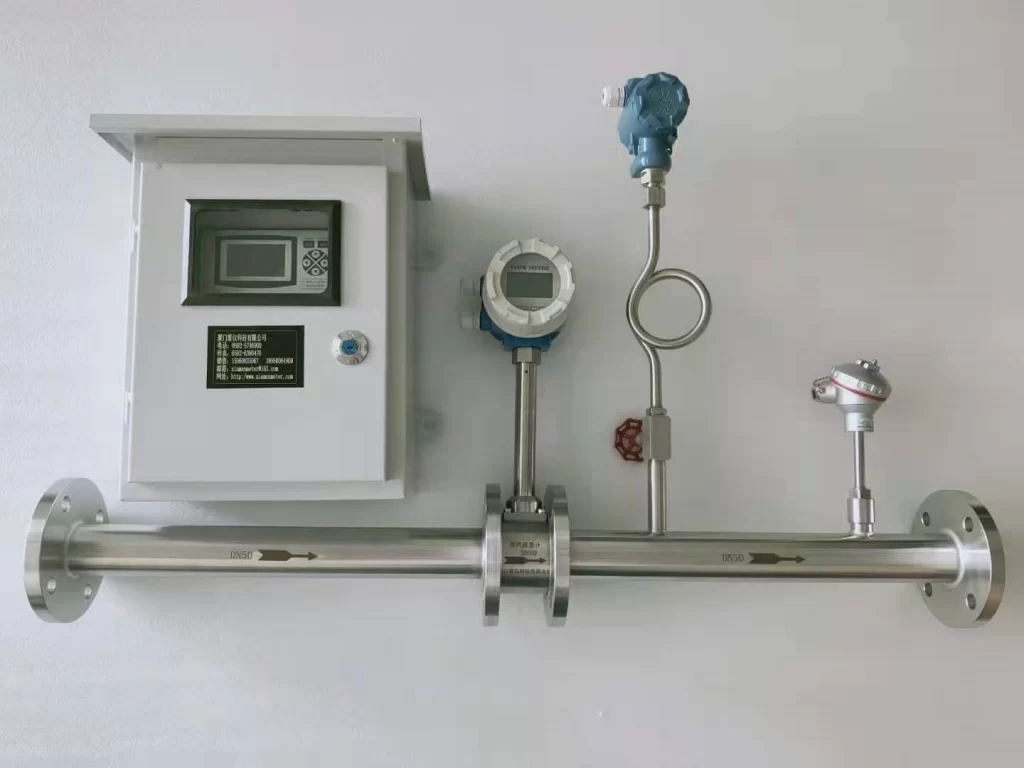
Principles of flow meter temperature and pressure compensation
The principle of temperature compensation:
The flow meter’s output signal is corrected according to the temperature change of the fluid, allowing it to provide accurate flow or volume measurements at different temperatures. The commonly used temperature compensation method is to monitor the temperature of the fluid in real time through a temperature sensor and make corrections based on the temperature-flow meter output characteristic curve.
Principle of pressure compensation:
The output signal of the flow meter is corrected according to the pressure change of the fluid, so that it can provide accurate flow or volume measurement at different pressures. The commonly used pressure compensation method is to monitor the pressure of the fluid in real time through a pressure sensor and make corrections based on the pressure-flow meter output characteristic curve.
The function of temperature and pressure compensation
Improve the measurement accuracy and reliability of the flow meter and avoid measurement errors caused by temperature and pressure changes. Temperature and pressure compensation enables the flowmeter to provide accurate flow or volume measurement under different working conditions, and is suitable for the measurement requirements of a variety of fluids and working conditions.
Therefore, in actual flow measurement, temperature and pressure compensation is a very important technical means.
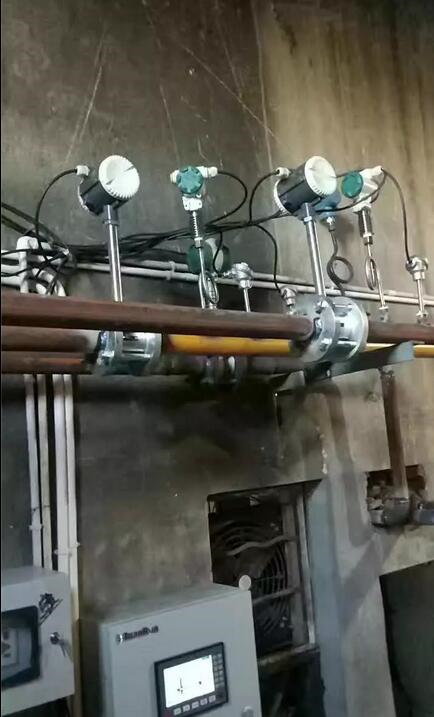
Which flow meters require temperature and pressure compensation?
Flow meters for the following measurement situations require temperature or pressure compensation:
- When measuring gas, temperature and pressure need to be compensated at the same time. Gases are generally settled based on standard volume flow rates. Because the volume flow rate of the gas changes when the temperature or pressure changes, the flow rate will change. For example, vortex flowmeters, gas turbine flowmeters, etc. are commonly used to measure gases.
- When measuring saturated steam, single temperature compensation or single pressure compensation is required. The density of saturated steam has a fixed relationship with temperature or pressure. Knowing any of these, the density of saturated steam can be determined.
- When measuring superheated steam, temperature and pressure need to be compensated at the same time. Steam is generally settled in terms of mass flow rate. Because either temperature or pressure changes, the density of the steam changes and the mass flow rate changes accordingly. For example, vortex flowmeters and differential pressure flowmeters are commonly used to measure steam.
- When measuring liquids, pressure compensation is generally not required. Below 5MPa, generally only the influence of temperature is considered, and temperature compensation is required for accurate measurement. In general measurements, no compensation can be used. Measuring some hydrocarbons (such as crude oil) generally requires temperature and pressure compensation at the same time.
Flowmeters that require temperature and pressure compensation mainly include the following types:
Volumetric flowmeter: A volumetric flowmeter calculates flow by measuring the volume of fluid passing through a pipe. Because fluids have different volumes at different temperatures and pressures, temperature and pressure compensation is required.
Mass flow meter: A mass flow meter calculates flow rate by measuring the mass of a fluid. Because fluids have different densities at different temperatures and pressures, temperature and pressure compensation is required.
Differential pressure flow meter: Differential pressure flow meter calculates the flow rate by measuring the pressure difference of the fluid in the pipeline. Since fluids have different densities and viscosity at different temperatures and pressures, which will affect the flow of the fluid, temperature and pressure compensation is required.
Vortex flowmeter: The vortex flowmeter calculates the flow rate by measuring the rotation frequency generated by the vortex in the pipe when the fluid passes through it. Since fluids have different densities and viscosity at different temperatures and pressures, which will affect the rotation frequency of the vortex street, temperature and pressure compensation is required.
Flowmeters that require temperature and pressure compensation need to be monitored and corrected based on actual conditions during installation and use to ensure measurement accuracy and reliability.
Implementation of temperature and pressure compensation
More featured Flow Measurement Solutions
- Application Case: Mass Flow Meter Measures Lime Slurry Flow and Density
- Guide: Types of Mass Flow Meters
- Fluid Flow Sensor | Types and Product List
- What Is Variable Area Flow Meter?
- Flowmeter Selection Guide | Find the Best One for Your Application
- 11 Flow Meter Types and Their Advantages and Disadvantages
- Pipe Flow vs Pressure – Relationship & Calculate Tools
- Top 4 Types of Pipeline Flow Meters-DN6~DN1000~DN6000
- Flow Measurement 101
Temperature and pressure compensation is the correction made by the influence of the measured object on the pressure and temperature measurement under a certain pressure and temperature. Usually when we measure gas flow, we pay more attention to temperature and pressure compensation, which is to obtain the flow rate under standard conditions by performing temperature and pressure compensation on the gas flow under working conditions.
Only by deeply understanding the mechanism of temperature and pressure compensation, applying it flexibly in work practice, and truly understanding the flow measurement can we not be passive in our work. If you have any technical questions about the temperature and pressure compensation of the flow meter, or need to purchase a gas flow meter, please feel free to contact us.