Best Technology Guide to Coriolis Mass Flow Meters.
Do you want to learn more about measurement technology for Coriolis mass flow meters? We will discuss and explain various measurement techniques for Coriolis mass flow meters.
Coriolis mass flow meter also called micro motion flow meter. Coriolis mass flow meter is the mass flow meter beasd on the coriolis force. Coriolis mass flow meter and thermal mass flow meter are the most common mass flow meters. Corolis mass flow meters are best choice for all process and custody transfer (CT) applications. Coriolis mass flow meter can measure different values at the same time. Mass, volume flow, density and concentration measurement of liquids and gases. This is the most important difference among Coriolis mass flow meter, DP and oval gear flow meters.
Featured Coriolis Mass Flow Meters
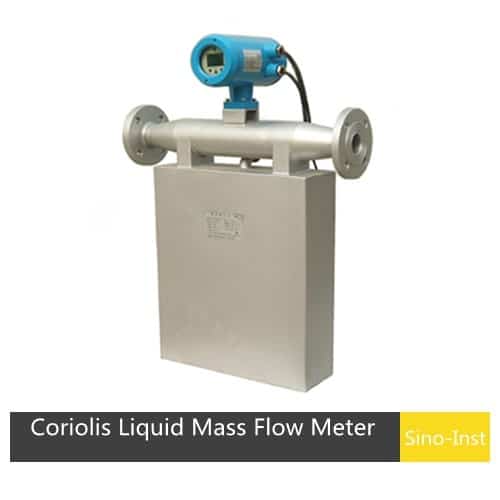
Coriolis Liquid Mass Flow Meter
SI-3504 Coriolis Liquid Mass Flow Meter, is the mass flow meter for liquid flow measurement. Like diesel fuel, and other liquid flow. Thermal mass flow meters are for gas flow measurement. Coriolis mass flow meters are for liquids. Si-3504 Coriolis Liquid Mass Flow Meter can be explosion proof type as customer need.
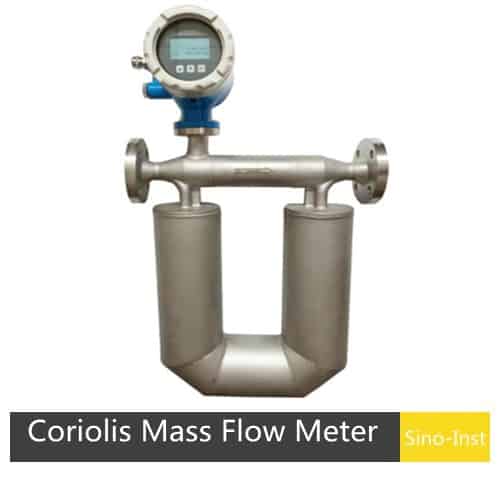
Coriolis Mass Flow Meter
SI-3505 Coriolis Mass Flow Meter is the leading precision flow and density measurement solution, offering the most accurate and repeatable mass measurement for liquids, or slurries. Coriolis Mass Flow Meter offers the most accurate measurement for virtually any process fluid, while exhibiting exceptionally low pressure drop.
- What is Mass Flow Meter?
- Working Principle of Coriolis Mass Flow Meter
- Advantages and Disadvantages of Coriolis Flow Meter
- Coriolis versus Thermal Mass Flow for Gases and Liquids
- Applications
- Application Cautions for Coriolis Mass Flowmeters
- How to Use Coriolis Mass Flowmeters
- Mass flow meter installation
- How do Coriolis meters measure density?
- Difference between mass flow meters and volume flow meters
- Technical Support
What is Mass Flow Meter?
A mass flow meter is a flow meter that measures the velocity of a fluid by measuring the mass of the fluid.
Methods of measuring fluid flow are: volume and mass.
The volume of a fluid is a function of fluid temperature and pressure and is a dependent variable. The mass of a fluid is a quantity that does not change with time, temperature, and pressure.
Among the commonly used flow meters, most are volume flow meters. Such as orifice flow meters, laminar mass flow meters, turbine flow meters. Vortex flow meters, electromagnetic flow meters. Rotor flow meters, ultrasonic flow meters. And oval gear flow meters, etc.
Common mass flow meters are: Coriolis mass flow meters and thermal mass flow meters.
What is Coriolis Mass Flow Meter?
Coriolis Mass Flowmeter is referred to as Coriolis force flow meter. Coriolis mass flow meter is a Coriolis force principle that uses fluid to flow in a vibrating pipe and is proportional to the mass flow rate. To measure mass flow directly. Coriolis mass flowmeters consist of a flow detection element and a converter. Coriolis mass flow meter realizes the direct measurement of mass flow. It has the characteristics of high accuracy, measurable multiple media and multiple process parameters. It is widely used in petrochemical, pharmaceutical, food and other industries.
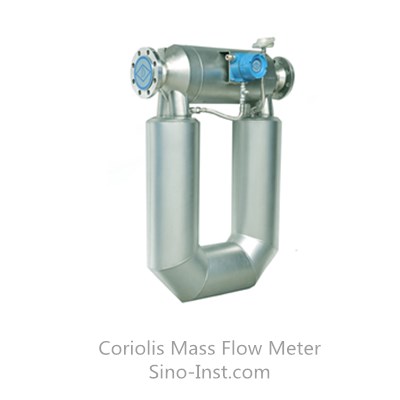
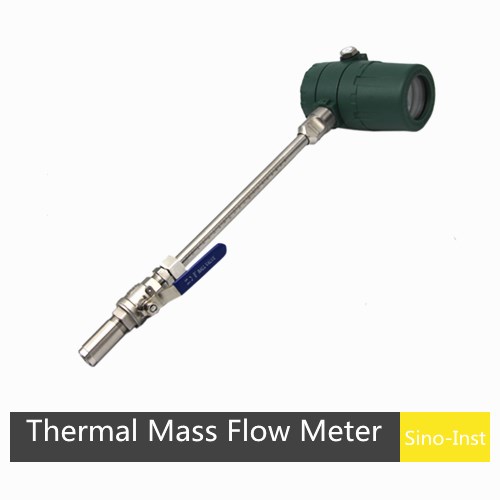
What is Thermal Mass Flow Meter?
Thermal mass flow meter (TMF for short) is also called thermal flow meter. Thermal mass flowmeters measure the mass flow of a fluid by using temperature field changes that occur when the fluid flows through a pipe heated by an external heat source. Or a flow meter that measures the mass flow of a fluid by using the relationship between the energy required for the fluid temperature to rise a certain value when heating the fluid and the mass of the fluid. Generally used to measure the mass flow of a gas. It has low pressure loss. Large flow range. High precision. High repeatability and high reliability. No moving parts, and can be used for monitoring and control of extremely low gas flow.
Mass flowmeters measure the mass flow of fluid without compensating for other parameters. Its most significant feature is that it can directly measure the mass flow of the medium without being affected by factors. Such as pressure and temperature in the working state of the medium.
Mass flow meter is a novel instrument that directly and accurately measures the mass flow of fluids.
The mass flow meter is classified as follows:
- Direct mass flow meter
That is, the quantity directly proportional to the mass flow is detected. And the detection element directly reflects the mass flow. - Derivative mass flowmeter
That is, a meter combined with a volume flow meter and a density meter is used to measure the mass flow rate. And the volume flow rate and the fluid density are detected at the same time. And an output signal related to the mass flow rate is obtained through calculation. - Compensated mass flowmeter
At the same time, the volume flow rate of the fluid and the temperature and pressure values of the fluid are detected. And then according to the relationship between the density of the fluid and the temperature and pressure, the density value of the fluid in this state is calculated by the calculation unit. And then the mass flow rate value of the fluid is calculated.
Working Principle of Coriolis Mass Flow Meter
Coriolis mass flow meter is a meter that directly measures mass flow by using the principle of Coriolis force. That is proportional to mass flow by fluid flowing in a vibrating tube.
Coriolis force flowmeter structure has many forms. Coriolis mass flowmeter generally consists of a vibrating tube and a converter. Vibration tube (measuring pipe) is a sensitive device. There are several shapes such as U-shape, Ω-shape, ring shape, straight tube shape, and spiral shape.
How Coriolis Mass Flowmeters Work?
- Coriolis mass flowmeters measure the force resulting from the acceleration caused by mass moving toward (or away from) a center of rotation.
- This effect can be experienced when riding a merry-go-round, where moving toward the center will cause a person to have to “lean into” the rotation so as to maintain balance.
- As related to flowmeters, the effect can be demonstrated by flowing water in a loop of flexible hose that is “swung” back and forth in front of the body with both hands. Because the water is flowing toward and away from the hands, opposite forces are generated and cause the hose to twist. They represent about 21% of all flowmeters sold.
- In a Coriolis mass flowmeter, the “swinging” is generated by vibrating the tube(s) in which the fluid flows.
- The amount of twist is proportional to the mass flow rate of fluid passing through the tube(s).
- Sensors and a Coriolis mass flowmeter transmitter are used to measure the twist and generate a linear flow signal.
Working Principle
A mass flow metering system includes a sensor and a transmitter for signal processing.
The mass flow meter is based on Newton’s second law: force = mass × acceleration (F = ma).
When a mass point of mass m moves at a speed V in a pipe rotating at an angular velocity ω to the P axis, the mass point is subject to two component acceleration
And its force:
(1) The normal acceleration, that is, the centripetal acceleration αr, whose magnitude is equal to 2ωr, faces the P axis;
(2) The tangential angular velocity αt, which is the Coriolis acceleration, is equal to 2ωV, and the direction is perpendicular to αr. Due to the compound motion, the Coriolis force Fc = 2ωVm acts in the αt direction of the particle, and the pipeline exerts a reverse force -Fc = -2ωVm on the particle.
When a fluid with density ρ flows at a constant velocity V in a rotating pipeline, any length of pipeline Δx will be subjected to a tangential Coriolis force ΔFc: ΔFc = 2ωVρAΔx (1)
In the formula, A is the cross-sectional area of the pipeline.
Because of the relationship: mq = ρVA
So: ΔFc = 2ωqmΔx (2)
Therefore, directly or indirectly by measuring the Coriolis force of a fluid flowing in a rotating tube, mass flow can be measured.
Advantages and Disadvantages of Coriolis Flow Meter
Advantages and Disadvantages of Coriolis Flow Meter | |
Advantages | Disadvantages |
Can handle sanitary applications | The cost is high, especially for line sizes above four inches. |
Approved for custody transfer and is highly reliable and low maintenance | |
Universal measuring principle for liquids and gases | Poor zero stability which affects the flow meter accuracy. |
Multivariable measurement – simultaneous measuring of mass flow, density, temperature and viscosity | |
High measuring accuracy: typically ±0.1% o.r., optionally: ±0.05% o.r. (PremiumCal) | It cannot be used to measure fluids with lower density, such as low pressure or low density gas. |
Measuring principle independent of the physical fluid properties and the flow profile | |
No inlet/outlet runs necessary. Generally, it is not required straight pipe lines when installing the sensor. | Slightly higher gas content in the liquid may cause a significant increase in measurement error. |
It has a wide range of measurable fluids. Including high viscosity fluids, liquid-solid two-phase fluids, liquid-gas two-phase fluids containing trace gases. And medium and high pressure gases of sufficient density. | |
The change in fluid viscosity has no significant effect on the measured value. | It is sensitive to external vibration interference. |
The change in fluid density has little effect on the measured value. | |
Bidirectional flow measurement | It cannot be used for larger diameters. Currently max size we can make is 8 inch Coriolis flow meter. |
It can take measurement of high viscosity fluids, such as crude oil, heavy oil, residual oil and other liquids with higher viscosity. | |
Pressure drop can be a consideration for “U” shaped tube designs and high viscosity fluids. | The pressure loss is large, especially when measuring a liquid with a high saturated vapor pressure. The pressure loss may cause vaporization of the liquid, and cavitation occurs. |
Coriolis versus Thermal Mass Flow for Gases and Liquids
- Fluid independent flow measurement and control – no need for recalibration
- Gas and liquid can be measured with the same sensor
- Ability to measure undefined or variable mixtures
- Suitable for supercritical fluids, e.g. carbon dioxide (CO2) or ethylene (C2H4)
- Same compact footprint
- High accuracy ± 0.2% of rate ± zero stability for liquids ± 0.5% of rate ± zero stability for gases
- Large turndown range of up to 1:2000
- Fast sensor response time: down to 50…100 msec
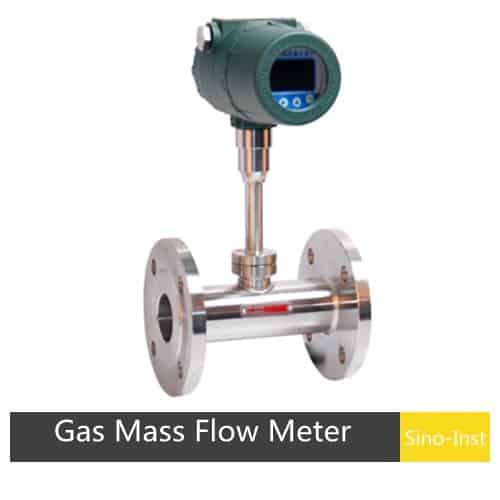
Applications
Coriolis mass flow meters are the best choice for applications like:
- Food & Beverage
- Pulp and paper
- Petrochemical
- Oil & Gas
- Power
- High Viscosity
- Paint
- Mining
- Process Control
- Water and wastewater
- And numerous other industries
Application Cautions for Coriolis Mass Flowmeters
- If the pressure drop is acceptable, operate a Coriolis mass flowmeter in the upper part of its flow range because operation at low flow rates can degrade accuracy.
- Note that high viscosity fluids increase the pressure drop across the flowmeter.
For liquid flows, make sure that the flowmeter is completely full of liquid. Be especially careful when measuring gas/vapor flow with Coriolis mass flowmeters. - Pay special attention to installation because pipe vibration can cause operational problems.
How to Use Coriolis Mass Flowmeters
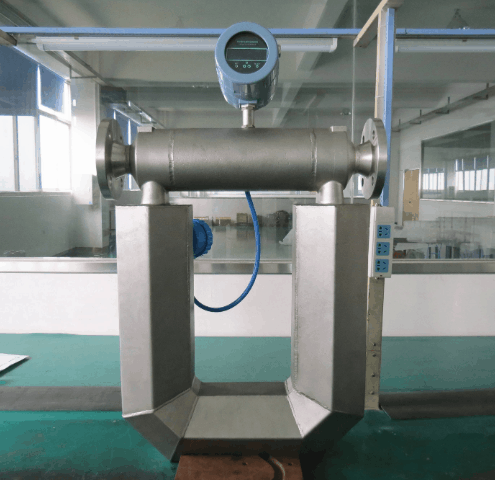
- Coriolis mass flowmeters measure the mass flow of liquids. Such as water, acids, caustic, chemicals, and gases/vapors. Because mass flow measured, the measurement is not affected by fluid density changes.
- Be particularly careful when using Coriolis mass flowmeters to measure gas/vapor flows. Because flow rates tend to be low in the flow range (where accuracy is degraded).
- Also, in gas/vapor applications. Large pressure drops across the flowmeter and its associated piping can occur.
- This flowmeter can be applied to sanitary, cryogenic, relatively clean. And corrosive liquids and gases/vapors in pipes smaller than 6-12 inches.
- General applications are found in the water, wastewater, mining, mineral processing. Power, pulp and paper, petroleum, chemical, and petrochemical industries.
- Materials of construction are generally limited to stainless steel and Hastelloy C.
- Straight-tube designs are available to measure some dirty and/or abrasive liquids.
- Many applications for Coriolis mass flowmeters are found in chemical processes. Where fluids can be corrosive and otherwise difficult to measure.
- Besides, the relative insensitivity to density allows Coriolis mass flowmeters to be applied in applications. Where the physical properties of the fluid are not well known.
- These flowmeters can also be used in chemical feed systems found in most industries.
Mass flow meter installation
In order for Coriolis mass flowmeters to work properly, safely, and with high performance, it is important to install and use them properly. This includes mechanical installation, electrical installation, and maintenance.
(1) Installation
Mechanical installation should pay attention to the following issues:
a. The flow sensor should be installed on a solid foundation. The small-diameter mass flowmeter with an inner diameter of less than 10mm is installed on a balanced, hard and vibration-free bottom surface. Such as a wall, a floor, or a special foundation. If it is used in a high-vibration environment, it should pay attention to the vibration absorption of the foundation. And a flexible pipe connection should be used between the sensor inlet and outlet and the pipe. The larger-diameter flowmeter is directly installed on the process pipeline. And the flowmeter should be installed with a pipe card and support Firmly fixed.
b. In order to prevent mutual influence between CMFs, when multiple flowmeters are used in series or in parallel. The distance between each flow sensor should be far enough. And the pipe card and support should be set on their own independent basis.
C. In order to ensure that no residual gas or liquid will accumulate in the flow sensor during use. For the elbow type flowmeter, when measuring liquid, the elbow should face down. And when measuring gas, the elbow should face up. When measuring the slurry or discharged liquid, the sensor should be installed in a vertical pipe with the flow from bottom to top. For straight-tube type flowmeters, avoid installing on the highest point when installing horizontally to avoid accumulation of air mass. When connecting the sensor and the process pipeline, stress-free installation must be done. Especially for the flow sensor of some straight pipe measuring tubes.
(2) Use and maintenance
① Zero adjustment of flowmeter. After the flow sensor is filled with the measured fluid, close the downstream valve of the sensor, and adjust the zero point of the flow meter under the condition of close to the working temperature. It is very important to ensure that the downstream valve is completely closed when adjusting the zero point and that no fluid is leaking. If the valve is leaking during zeroing, it will cause a large error in the entire measurement.
② Set the flow and density calibration coefficients. It is important to set the flow and density calibration coefficients to work correctly. The flow calibration coefficient represents the sensitivity of the sensor and the flow temperature coefficient. The sensitivity indicates how much flow is measured every microsecond.
(The unit is usually g / s); the flow temperature coefficient indicates the degree of influence of the sensor’s elastic modulus on temperature. These are directly related to the measurement accuracy of the flow meter. The density calibration coefficient represents the natural vibration period (unit is often microseconds) and the density temperature coefficient of the sensor when the tube is air and the tube is water at 0 ° C. Obviously, these are related to the measurement. The accuracy of density is directly related.
③ Maintain the flowmeter in normal operation during use. It is important for the flowmeter to work in time to find faults and eliminate faults in time. The following faults are common in actual work:
a. No output: Refers to the flow through the sensor and the sensor has no signal output;
b. Output does not change: Although the flow rate has changed, the output remains unchanged;
c. The output is abnormal, the output changes randomly, and has nothing to do with the change of the flow, that is, the output is abnormal;
d. There is output intermittently: intermittent output, irregular start and end, but when there is output, the output signal can reflect correctly
The amount of traffic.
The above fault conditions should be carefully checked and eliminated, and the manufacturer should be repaired if necessary.
How do Coriolis meters measure density?
The mass flow meter uses the Coriolis principle. The phase difference between the vibration frequency of the lower half of the measuring tube is proportional to the mass flow rate to measure the flow rate. And the density is calculated using the function relationship between the resonance frequency of the measuring tube and the density of the measured medium in the tube.
From these two basic parameters, mass flow rate qm and density ρ, the volume flow rate qv (= qm / e) is derived.
If the measured liquid is two kinds of mixed liquids that are miscible or immiscible with a certain density difference, a density calculation will yield one. The concentration of this liquid in the mixed liquid. Such as the water content of the oil-oil-water mixed liquid, can be measured in the measurement of liquid-solid two-phase flow.
From the principle, it can be known that in the flow measurement industry. The mass flow meter can directly measure the mass flow of the fluid medium without compensating for other parameters. Its most significant feature is that it can directly measure the mass flow of the medium without being affected by factors. Such as pressure and temperature in the working state of the medium.
The density measurement principle of Coriolis mass flowmeter is that the vibration frequency is inversely proportional to the square root of the fluid density. And the fluid density is determined by measuring the vibration frequency.
So, the mass flow meter can realize the measurement of fluid mass flow and the measurement of fluid density.
Difference between mass flow meters and volume flow meters
The ranges of thermal mass flow meters for gases are specified in such units as ln/min, sccm or m3n/h. These units look like volumetric units, but in truth they are expressions of Mass Flow. What is the story behind this?
Imagine you have a cylinder of 1 litre, which is closed by means of a moveable piston of negligible weight. This cylinder contains 1 litre of air at ambient pressure, approx. 1 bar. The weight of this volume of air at 0°C is 1.293 g, this is the mass. When we move the piston half way to the bottom of the cylinder, then the contained volume of air is only ½ litre, the pressure is approx. 2 bar, but the mass is unchanged, 1.293 g; nothing has been added, or left out.
Following this example, mass flow should actually be expressed in units of weight such as g/h, mg/s, etc. Most users, however, think and work in units of volume. No problem, provided conditions are agreed upon, under which the mass is converted to volume.
Following the ‘European’ definition, a temperature of 0°C and a pressure of 1,013 bar are selected as “normal” reference conditions, indicated by the underlying letter “n” in the unit of volume used (mln/min, m3n/h).
Alternative, a temperature of 20°C and a pressure of 1,013 bar are used to refer to “standard” reference conditions, indicated by the underlying letter “s” in the unit of volume used (mls/min, m3s/h). Please be aware of this, because if the difference is not considered, it may lead to an error of 7%!
According to the ‘American’ definition the prefix “s” in sccm, slm or scfh refers to “standard” conditions 101.325 kPa absolute (14.6959 psia) and temperature of 0°C (32°F).
Volumetric measuring devices, like variable area meters or turbine flow meters, are unable to distinguish temperature or pressure changes.
Mass flow measurement would require additional sensors for these parameters and a flow computer to compensate for the variations in these process conditions. Thermal mass flow meters are virtually insensitive to variations in temperature or pressure.
Technical Support
The ability a flow meter to accurately measure and control flow is essential in maintaining the process conditions required to maximize plant production, efficiency and product quality. Oftentimes, flow measurements are used as indicators of overall process performance. This is due to the law of conservation of mass which states that the mass entering a system is equal to the mass leaving the system when both are measured over the same interval. Therefore, mass flow meters and mass flow transmitters become crucial in overall plant operations.
The relationship between mass flow and volumetric flow is as follows: Mass Flow Rate = Density x Volumetric Flow Rate
Although volumetric flow under nominal conditions may be accurately calculated, the process conditions and fluid properties can vary sufficiently such that it is questionable if the measured volumetric flow rate (or derived using velocity) represents the required mass flow rates. Process conditions such as density and viscosity, and their effect on the accuracy of flow measurement must be taken under consideration. The effects of temperature on density of fluids vary widely. Gases and steam are most affected while solids are least affected, and liquids generally range somewhere in between. The effects of pressure on the density of solids are negligible because both are non-compressible. However, liquids requiring higher accuracies (better than ±1%) such as fuel monitoring, mass balancing of liquids and others require liquid mass flow meters. Please go to Industrial Measurement Applications for applications requiring Coriolis flow meters. However, the effect of pressure on the density of gases and steam is considerable. The sino-inst thermal mass flowmeters for gases are ideal for accurately monitoring mass flow of gases, while our ALVT-mass flow meters are ideal for direct steam flow meter measurement.
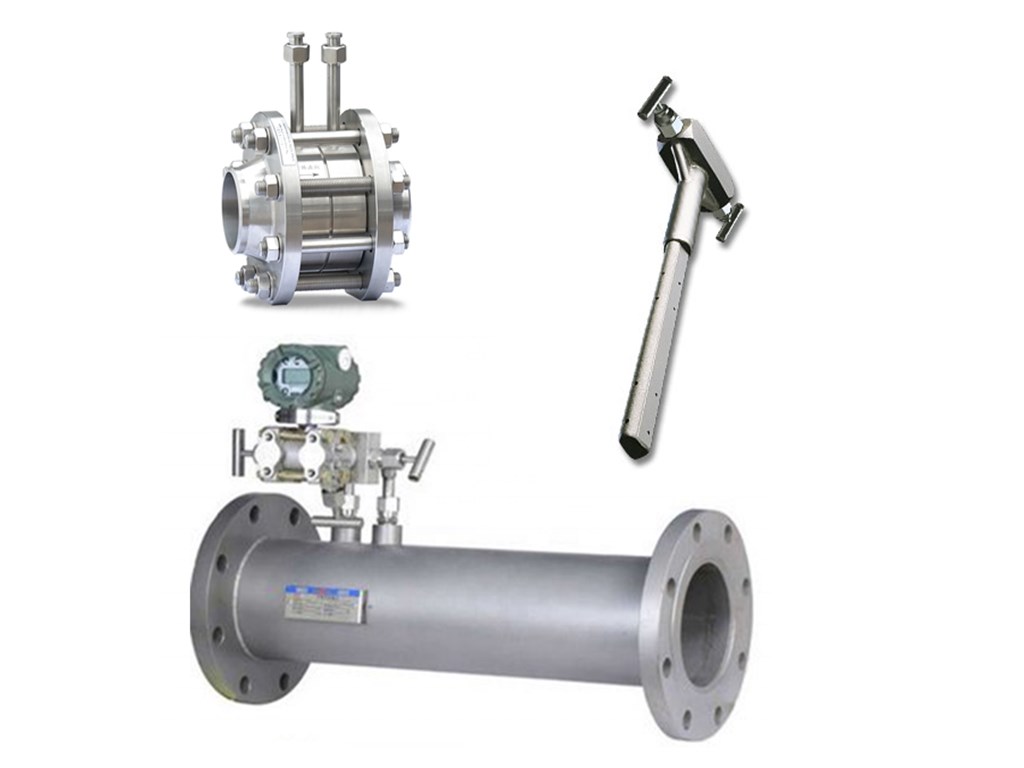
Differential Pressure Flow Meter Technology
Differential Pressure Flow Meters also called DP flow meters. Differential pressure flow meters consist of flow sensors and pressure/differential transmitters. DP Flow Meters measure the flow rate based on the differential pressure measured by the flow sensor parts. Flow sensors are the important part of differential pressure flow meters. Like: Orifice plate, Venturi tube, Wedge, V-cone and Averaging Pitot Tubes. Differential pressure (DP) flow meters are suitable for applicaitons, like: water, gas, steam, oil….
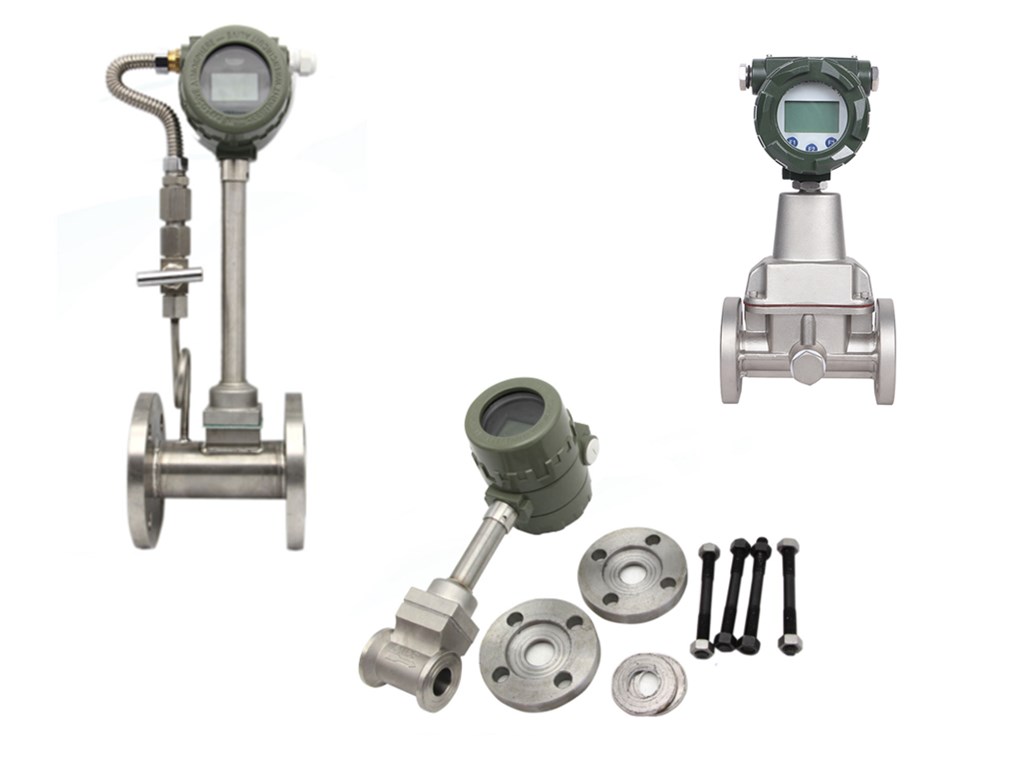
Vortex Flowmeter Technology
Vortex flow meters are suitable for measuring steam as well as a variety of liquids and gases. As fluid moves across a vortex meter shedder bar, vortices form. The frequency of the vortices shedding is proportional to the fluid velocity. Even for the steam flow rate, Vortex flow meters are the perfect choice. Pressure and Temperature compensation ensure measurement accuracy. When measure steam or gas flow in pipes with variable operating pressure and temperature. Applications in the chemicals and petrochemicals industries. For example, in power generation and heat-supply systems. Involve widely differing fluids: saturated steam, superheated steam, compressed air. Nitrogen, liquefied gases, flue gases, carbon dioxide, fully demineralized water. Solvents, heat-transfer oils, boiler feedwater, condensate, etc.
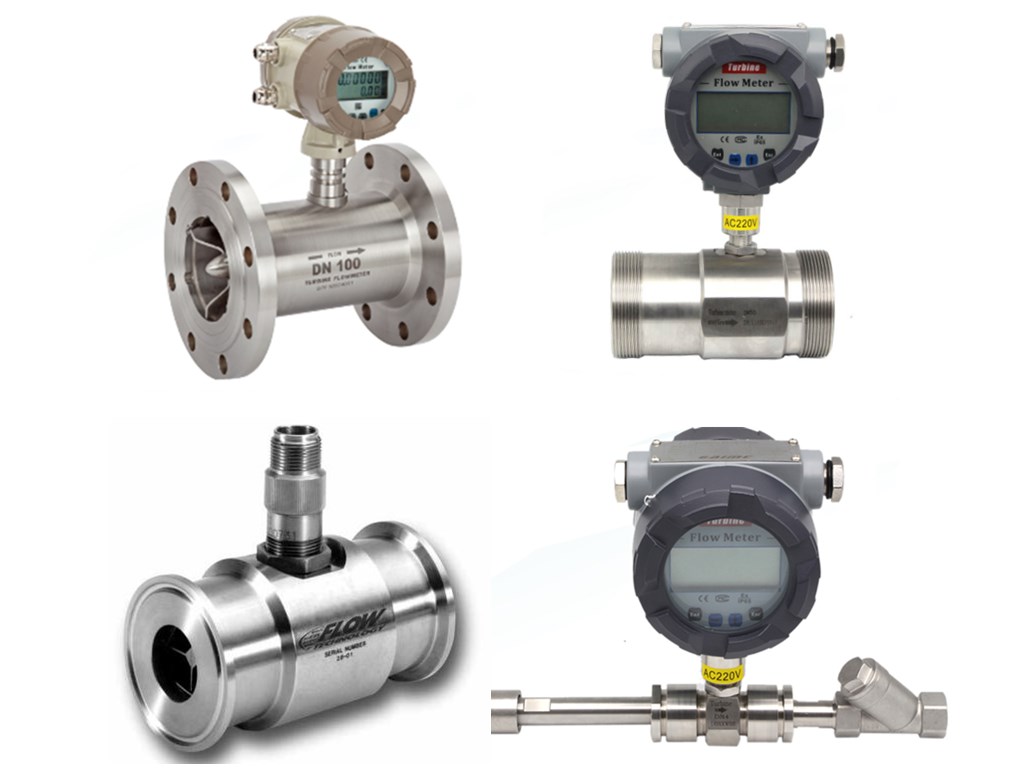
Turbine Flowmeter Technology
A turbine flow meter is a Volume flowmeter. Turbine flow meters use the mechanical energy of the liquid or gas to rotate a rotor in the flow stream. The velocity of the turbine rotor is proportional to the velocity of the fluid passing through the flow meter. The frequency of the signal relates directly to flow rate. The vaned rotor is the only moving part of the flow meter. Turbine flow meters measure the velocity of liquids, gases and vapors in pipes. Such as hydrocarbons, diesel, water, cryogenic liquids, air, and industrial gases. Turbine flow meter is the most popular equipment to measure flow electronically. They offer a wide flow and application rangeability. Turbine Flow Meters are easy to maintain, durable and versatile.