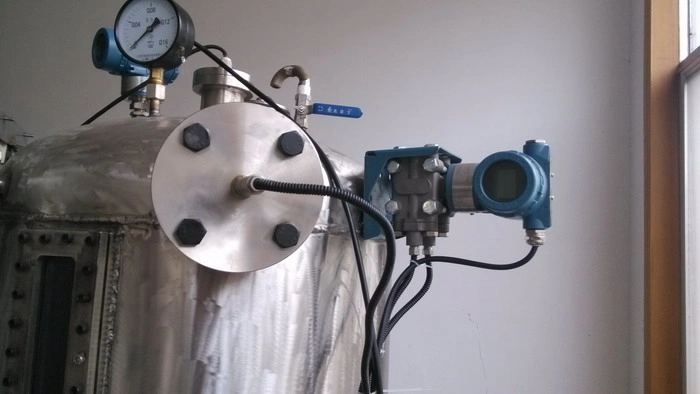
Pressure transmitters and differential pressure transmitters can be used to measure the level of liquids such as water or fuel in vented or sealed tanks. And in many special working conditions, it has advantages that other liquid level transmitters cannot match. For example, measurement of viscous, high-temperature, corrosive liquids or gases in vacuum tanks.
Measurement principle:
Tank Level Measurement is realized using a pressure transmitter or a differential pressure transmitter, both of which apply the static pressure principle of liquids.
The static pressure at a certain point in the liquid is proportional to the distance from the point to the liquid surface, that is: P = ρgh.
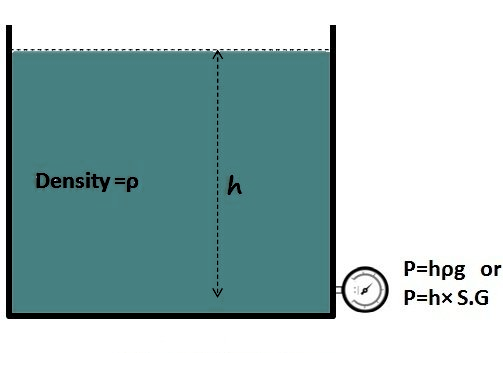
Among them: P-the pressure (pressure) of the measured point, ρ-medium density, g-gravitational acceleration, h-height from the measured point to the liquid surface.
For the determined measured medium ρ, g is a constant, so the change in the position of the measured point to the liquid surface is only related to the measured P pressure (pressure).
When measuring liquid level in an open container, a pressure transmitter is all you need.
When measuring the liquid level of a closed pressure vessel, you can consider using two pressure or one differential pressure transmitter, that is, one for lower limit measurement and one for upper limit measurement. Their output signals are subtracted to measure the liquid level. When the liquid level and pressure in the container remain unchanged, it can also be used to measure the density of the medium.
For differential pressure transmitters,
Let △P be the differential pressure signal received by the transmitter, P0 be the internal pressure of the container, P+ be the positive pressure side pressure of the transmitter, P- be the negative pressure side pressure of the transmitter; ρ be the density of the liquid in the container; g is the acceleration of gravity; h1 is the height from the process zero point to the pressure port on the upper part of the container; h2 is the process liquid level of the container; h is the height from the transmitter to the zero point of the process liquid level.
Then there are:
P+=P0+ρgh1+ρgh
P-=P0+ρgh2+ρgh
△P=P+-P-=ρgh1-ρgh2
When the liquid level changes from h2=0 to h2=h1, the differential pressure measured by the differential pressure transmitter changes from a large value to ΔP=0. By setting the transmitter, the output current changes from 4mA to 20mA.
Level measurement in vented/open tanks
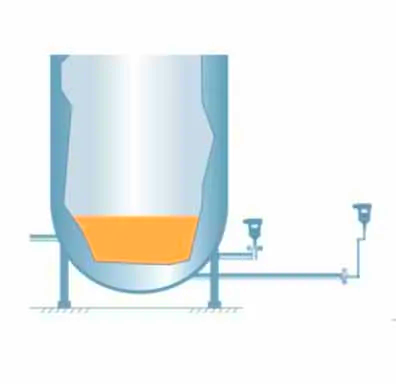
Open tank level measurement means the tank is open to the atmosphere. Any change in atmospheric pressure will affect the process fluid pressure inside the tank.
Use a pressure transmitter to measure the liquid level of vented/open tanks. Generally, the pressure transmitter is installed lower in the tank or connected to the pressure at the bottom of the tank. The transmitter can be equipped with flange or pressure pipe.
Of course, if the medium conditions permit, such as water measurement, then it may be cheaper to use a simple submersible level transmitter.
Single flange liquid level transmitter survey mode For viscous liquids or coagulable liquids, an isolation diaphragm should be added at the entrance of the pressure guiding pipe, and silicone oil should be filled in the pressure guiding pipe to transmit pressure with the help of silicone oil.
Sealed tank Level Measurement
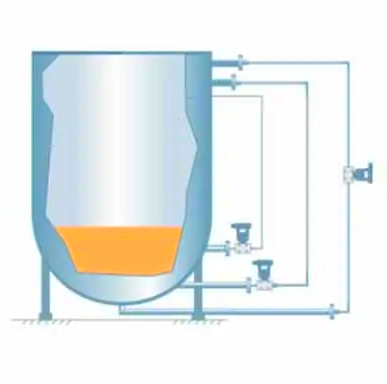
For closed vessels, because the interior is isolated from the atmosphere, the pressure within the tank may change from positive pressure to vacuum when the process fluid fills or empties the tank. This change in tank pressure will directly affect the measured level unless compensated for. This is done by connecting the low side pipe of the differential pressure transmitter to the top of the tank. Therefore, when measuring the liquid level of a closed tank, a differential pressure transmitter must be used.
The media in chemical production often encounter problems such as impurities, crystallized particles or agglomeration, which can easily block the connecting pipeline. In this case, a flange-type differential pressure transmitter can be used. The closed system composed of membrane box, capillary tube and measuring chamber is filled with silicone oil, which serves as a pressure transmission medium to prevent the measured medium from entering the capillary tube and transmitter to avoid clogging.
Example of calculation
Assume that ρ medium is the medium density = 1.5, ρ0 is the silicone oil density = 0.93, H0 is the medium mass range 0-5m, H1 = 1m, H2 = 6m. The double flange level gauge is installed below the horizontal line of the lower end flange of the closed vessel. Let’s calculate the measuring range of the differential pressure transmitter.
Measuring range: ΔP=ρ×g×H0=1.5×9.8×5=73.5KPa
High-pressure side empty liquid level pressure: P(+)=ρ0×g×H1=0.93×9.8×1=9.114KPa
Low-pressure side empty liquid level pressure: P(-)=ρ0×g×H2=0.93×9.8×6=54.684KPa
Pressure difference when the liquid level is empty: ΔP= P(+)-P(-)=9.114-54.684=-45.57KPa
Pressure difference when full liquid level: ΔP=empty liquid level pressure difference ΔP+range value ΔP=-45.57+73.5=27.93KPa
Therefore, the measuring range of the differential pressure transmitter is: -45.57 to 27.93KPa
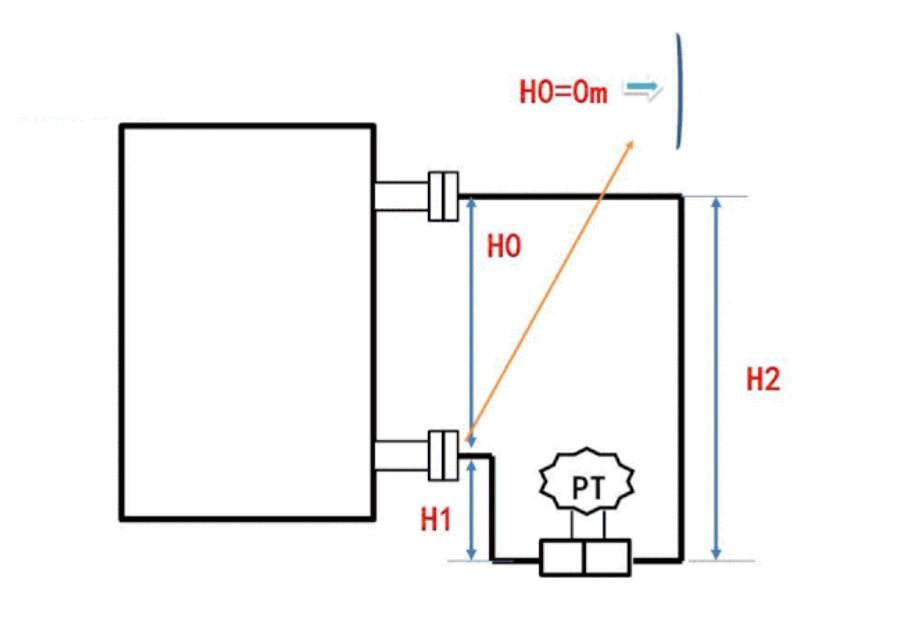
Featured Pressure Transmitters/DP Transmitters for Tank Level Measurement
Using pressure transmitters and differential pressure transmitters to measure tank liquid level can meet many special working conditions. For example:
- Larger size tanks;
- High temperature medium;
- Highly viscous media;
- Extremely low temperature medium;
- Corrosive media;
- Volatile media, etc.;
Of course, different measurement media and tank parameters will have an impact on the selection of the transmitter. Including diaphragm material, specifications, thickness, filling liquid type, capillary length and inner diameter, etc. Various factors should be considered comprehensively when selecting.
In many Tank Level Measurement working conditions, we will first use the liquid level transmitter. For example, ultrasonic level meter, radar level meter, etc. Pressure transmitters and differential pressure transmitters also have incomparable advantages. If you need to perform Tank Level Measurement and have related purchasing needs, please feel free to contact our sales engineers!