Turbine Flow Meter Overview
Turbine flow meters are cost-effective and offer reliable, minimal flow meter maintenance required.
Turbine Flow Meters Benefits
- Simple, durable design
- Easy installation and maintenance
- Reliable operation under a wide range of temperatures and pressures
- Turndown ratio is up to 35:1
- Good level of accuracy at an economic price
- Wide variety of process connections
- Low pressure drop
Quick Specifications
Diameter | DN4-DN200 |
Accuracy | ±0.1%,±0.5%,±0.2%(Optional) |
Temp. range | -20~+150℃ (OEM) |
Connection | Thread, flange, tri-clamp |
Output | Pulse, 4-20mA analog output, RS485 (Modbus-RTU protocol), HART |
Protection | IP65 or IP68 (Optional) |
Explosion proof | Exia‖CT4 or Exd‖BT6 |
Type Select of Turbine Flow Meters
And after understanding the application several factors come into effect when choosing a flow meter, such as:
- Fluid Type
- Viscosity
- Connection
- Pipe Sizing
- Process Temperature (min & max)
- Flow Range (min & max)
- Pressure Range (min & max)
- Accuracy Range
- Specific Application
- Sanitary or not
- Local display
- Singal output
If you need volumetric total flow and/or flow rate measurement, a turbine flow meter is the ideal device. Turbine flow meters are used in a wide variety of liquid and gas flow sensing applications. They can be built to endure high pressure, and high and low temperatures. They offer a high turn-down with minimum uncertainty and excellent repeatability. Turbine flowmeters are also simple to install and maintain only requiring periodic recalibration and service.
Turbine Measuring Principle
Theory of Operation
Turbine Flow Meter Equation
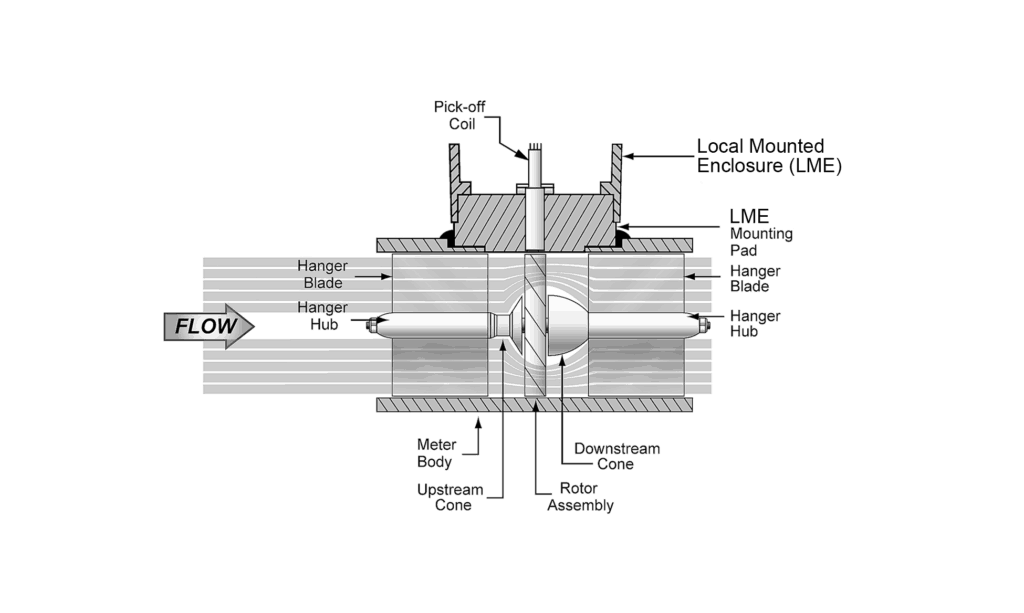
Totalizing Flow
Achieving Repeatability
How Turbine Flowmeters Work
Advantages & Disadvantages of Turbine Flow Meters
Turbine Meter Advantages | Turbine Meter Disadvantages |
Wide flow rangeability including low flow rates | Requires constant backpressure to prevent cavitation |
Turndown ratio is up to 35:1 | Accuracy adversely affected by bubbles in liquids |
Good level of accuracy at an economic price | Turbine meters can be used with clean liquids and gases
only |
Simple, durable construction | Not applicable for measuring corrosive fluids |
Easy to install and maintain | Requires a
turbulent flow profile (consistent fluid velocity across the pipe diameter)
for accuracy |
Flexible connection to flow instruments for flow control | Sensitive to changes in fluid viscosity |
Wide variety of process connections | Require a
straight run of pipe before and after the turbine meter to allow swirl
patterns in the flow stream to dissipate |
Turbine meters can operate over a wide range of
temperatures and pressures | |
Low pressure drop across the turbine | May not
function properly with high viscosity fluids where the flow profile is
laminar |
Provides a convenient signal output |
Applications for a Turbine Flow Meter
A turbine flow meter measures the velocity of liquids, gases and vapors in pipes.
Such as:
- Oil and gas;
- Water and wastewater;
- Gas utility, chemical, power, food and beverage, aerospace, pharmaceutical;
- Metals and mining;
- Pulp and paper.
- Fiscal and custody transfer, check metering or blending/batching;
- Rude oil production;
- Floating production, storage and off-loading (FPSO), refined product loading and offloading;
- Tank farm/storage inventory control;
- Hydrocarbons in fuel flow measurement;
- Chemical flow metering;
- Cryogenic liquid flow metering;
- Air or gas flow metering;
- General industrial flow metering;
- Hydrocarbons and natural gas;
- Low viscosity applications: Tap and demineralized water. Fuel flow meter solvents, Pharmaceutical fluids.
The repeatability of the meters ensures quality measurement. Over a wide range of flow rates, temperatures, compositions and viscosities.
High accuracy turbine flowmeters are available for custody transfer of hydrocarbons and natural gas.
A mass flow computer is often used in custody-transfer applications to correct for pressure, temperature and fluid properties. To achieve the desired accuracy.
Industries Where Used
- Water injection
- Test and production separators
- Disposal wells
- Hydraulic fracturing
- Chemical injection
- Natural gas pipelines
- Engine Testing
- Fuel flow measurement
- Shipboard reverse osmosis systems
- Monitor fuel supply to ship engines
- Sanitary measurement
- Pill coating
- Custody transfer
- Building automation
- HVAC
- Water metering
- Liquids measurement for plant applications and truck deliveries
How to Use Turbine Flowmeters
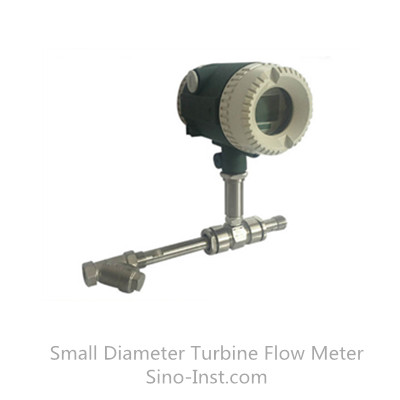
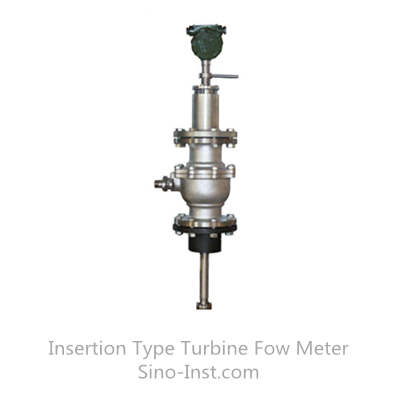
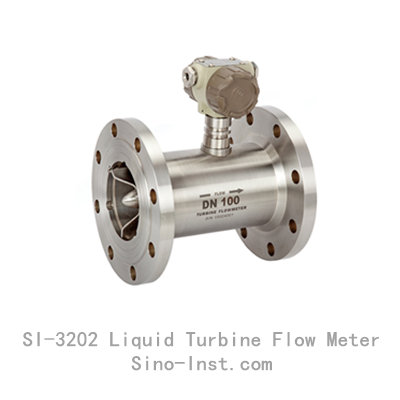
Turbine flowmeters measure the velocity of liquids, gases and vapors in pipes. Such as hydrocarbons, chemicals, water, cryogenic liquids, air, and industrial gases. For custody transfer of hydrocarbons and natural gas. High accuracy turbine flowmeters are available. These flowmeters often incorporate the functionality of a flow computer. To correct for pressure, temperature, fluid properties and achieve desired accuracy for application.
Be careful using turbine flowmeters on fluids that are non-lubricating. Because the flowmeter can become inaccurate and fail if its bearings prematurely wear. Some turbine flowmeters have grease fittings for use with non-lubricating fluids. Besides, turbine flowmeters that are designed for a specific purpose. Such as for natural gas service, can often operate over a limited range of temperature (such as up to 60ºC). Whereby operation at higher temperatures can damage the flowmeter.
This flowmeter can be applied to sanitary, relatively clean, and corrosive liquids in sizes up to approximately 24 inches. Smaller turbine flowmeters can be installed in the piping. But larger turbine flowmeters require the installation of substantial concrete foundations and supports. The flow of corrosive liquids can be measured with proper attention to the materials of construction of all wetted parts. Such as the body, rotor, bearings, and fittings.
Applications for turbine flowmeters are found in the water, petroleum, and chemical industries. Water applications include distribution systems within and between water districts. Petroleum applications include the custody transfer of hydrocarbons. Miscellaneous applications are found in the food and beverage, and chemical industries.
Application Cautions for Turbine Flowmeters
Turbine flowmeters are less accurate at low flow rates due to rotor/bearing drag that slows the rotor. Make sure to operate these flowmeters above approximately 5 percent of maximum flow. Turbine flowmeters should not be operated at high velocity. Because premature bearing wear and/or damage can occur. Be careful when measuring fluids that are non-lubricating. Because bearing wear can cause the flowmeter become inaccurate and fail. In some applications, bearing replacement may need to be performed routinely. And increase maintenance costs. Application in dirty fluids should generally be avoided so as to reduce the possibility of flowmeter wear and bearing damage. In summary, turbine flowmeters have moving parts that are subject to degradation with time and use.
Abrupt transitions from gas flow to liquid flow should be avoided. Because they can mechanically stress the flowmeter, degrade accuracy, and/or damage the flowmeter. These conditions generally occur when filling the pipe and under slug flow conditions. Two-phase flow conditions can also cause turbine flowmeters to measure inaccurately.
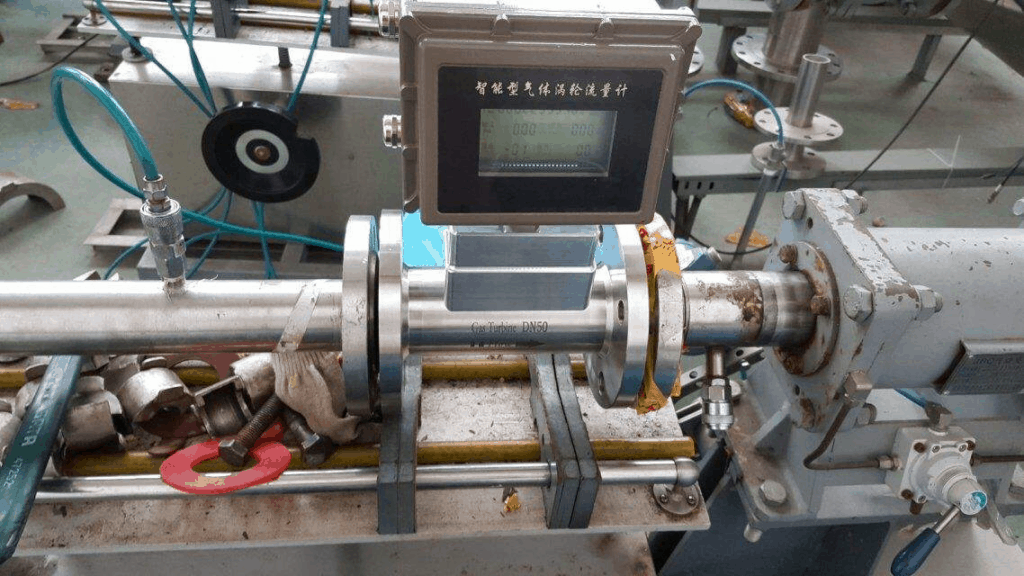
Turbine Flow Meter Calibration
“To calibrate” means “to standardize (as a measuring instrument) by determining the deviation from a standard so as to determine the proper correction factors.” There are two key elements to this definition: Determining the deviation from a standard. And ascertaining the proper correction factors.
Flow meters need periodic calibration. This can be done by using another calibrated meter as a reference or by using a known flow rate. Accuracy can vary over the range of the instrument. And with temperature and specific weight changes in the fluid, which may all have to be taken into account.
Thus, the meter should be calibrated over temperature as well as range. So that the appropriate corrections can be made to the readings. A turbine meter should be calibrated at the same kinematic viscosity at which it will be operated in service. This is true for fluid states, liquid and gas.
In Volumetric Method technique, flow of liquid through the meter being calibrated is diverted into a tank of known volume. The time to displace the known volume is recorded to get the volumetric flow rate eg:- gallons per minute. This flow rate can then be compared to the turbine flow meter readings.
Turbine Flow Meter Price
Sino-Inst is a Turbine flow meter manufacturer, China. Sino-Inst offers over 10 turbine flow meter products. A wide variety of turbine flow meter options are available to you, such as free samples, paid samples. The price of turbine flow meters are decided by flollowing factors:
- Pipe diameter;
- Flow range;
- Measured medium;
- Whether it is corrosive;
- Whether explosion protection is required;
- Whether it needs local display;
- Connection method;
- Measure pressure;
- Measure temperature;
- Signal output;
- Accuracy requirements;
- Material requirements;
For example, Model DN15 Turbine flow meter’s price is around USD 140.00/pc.
Gas Turbine Flow Meter
Low Flow Turbine Flow Meter
How do you calculate K factor for a turbine flow meter?
There are two different manufacturers k:
one is k = f / Q, which is the number of vortices generated per unit flow;
the other is k = Q / f, which is the flow corresponding to each vortex.
The k value is calibrated by the factory water.
The number of vortices of the sensor measuring instrument is compared with the volume flow measured by the calibration device to obtain the k value.
The value of k is actually related to the mechanical structure inside the measuring tube of the flow meter.
Take k = f / Q as an example, the formula is as follows:
Where
D —- Measuring tube diameter
St —- Strauhal number, constant in a certain range of Reynolds number
d —- characteristic width of vortex generator
m–the ratio of the arcuate area on both sides of the vortex generator to the cross-sectional area inside the pipe
The values of d and m are difficult to measure accurately, so it is difficult to obtain accurate k values by calculation.
A liquid flow meter is a device used to measure the volumetric, mass, nonlinear and linear flow rate of a liquid. The flow rate is calculated by measuring the liquid’s velocity. There are many types of liquid flow meters. The type selected will depend on the application and type of liquid. The nature of the fluid and the installation will impact the type of liquid flow meter selected.
Applications of Liquid Flow Meters
There are five types of liquid flow meters:
Differential Pressure, Velocity, Positive Displacement, Mass and Open Channel.
Differential Pressure Flow Meters
Examples of differential pressure flow meters include venture tubes, orifice plates. Flow nozzles, elbow-tap meters, pilot tubes, variable area meters and target meters.
Differential pressure flow meters are most commonly used to determine a liquid’s flow rate. Nearly 50% of the world’s flow meters consist of this type. They operate on the principle that when the pressure drops across the flow meter, it proportional to the square number of the flow rate. To determine the flow rate, the pressure differential is measured and then the square root is taken.
Differential pressure flow meters have a primary and secondary part. The primary part causes a change in movement energy, adding to the differential pressure within the pipe. The secondary part calculates the pressure differential and gives the signal read-out which is converted to the flow value.
Velocity Flow Meters
Examples of velocity flow meters include turbine, vortex shedding, swirl. Conada Effect & Momentum Exchange, electromagnetic, ultrasonic, Doppler and Transit time.
In a velocity flow meter, flow is determined by measuring the speed at more than one flow point and then integrating the speed over the entire flow area.
Turbine flow meters are used in petroleum pipelines. They detect leaks along the pipeline. Turbine meters are also used to load light hydrocarbon products into rail cars and road tankers. They also meter chemicals, fuel and water used in oil drilling processes.
Positive Displacement Flow Meters
Examples of positive displacement flow meters include reciprocating piston. Oval gear, nutatingdisk and rotary vane.
In a positive displacement flow meter, fluid flow is measured by precisely fitted rotors. Fixed and known volumes are shifted between the rotors. The spinning of the rotors is proportional to the volume of the displaced fluid. The amount of rotations is counted by an integral electronic pulse transmitter. This information is then converted into flow rate and volume.
Positive displacement flow meter are used to measure the flow rate of fluids such as polymer additives, lubrication oils, heating oils, vegetable and animal fat, printing ink and dichlorodifluoromethane R-12.
Mass Flow Meters
Examples of mass flow meters include Coriolis and thermal. Of the two types, the Coriolis meter is the most used. They were developed in response to the need for higher accuracy levels in flow measurement of mass related processes such as heat transfers and chemical reactions.
Mass flow meters are used in pharmaceuticals, mining, power industries and in waste water.
Open Channel Flow Meters
The Weir and Flume are two types of open channel flow meters.
Open channel refers to any area within which the liquid flows. Examples include non-pressurized sewers, tunnels, canals, rivers and streams. To monitor open-channel flows, depth-related methods are frequently used. The instantaneous flow rate can be calculated by measuring the depth of the water.
Liquid flow meters play an integral role in industrial applications. The type chosen will depend on the application.
A vortex flow meter is a flow measurement device best suited for the introduction of moving parts presents problems. They are available in industrial grade, brass or all plastic construction. Sensitivity to variations in the process conditions are low and with no moving parts. Vortex flow meters have relatively low wear compared to other types of flow meters.
Vortex flow meters operate under the vortex shedding principle. Where an oscillating vortexes occur when a fluid such as water flow past a bluff (as opposed to streamlined) body. The frequency that the vortexes are shed depend on the size and shape of the body. It is ideal for applications where low maintenance costs are important. Industrial size vortex meters are custom built and require appropriate sizing for specific applications.
Positive displacement flowmeter directly measures the volume of the fluid passing through the flowmeter. Positive displacement flowmeters achieve this by repeatedly entrapping fluid in order to measure its flow. This process can be thought of as repeatedly filling a bucket with fluid before dumping the contents downstream. The number of times that the bucket is filled and emptied is indicative of the flow through the flowmeter. Many positive displacement flowmeter geometries are available.
Entrapment is usually accomplished using rotating parts. That form moving seals between each other and/or the flowmeter body. In most designs, the rotating parts have tight tolerances. So these seals can prevent fluid from going through the flowmeter without being measured (slippage). In some positive displacement flowmeter designs, bearings are used to support the rotating parts. Rotation can be sensed mechanically or by detecting the movement of a rotating part. When more fluid is flowing, the rotating parts turn proportionally faster. The transmitter processes the signal generated by the rotation to determine the flow of the fluid. Some positive displacement flowmeters have mechanical registers that show the total flow on a local display. Other positive displacement flowmeters output pulses that can be used by a secondary electronic device to determine the flow rate.
Positive displacement flowmeters can be applied to clean, sanitary, and corrosive liquids. Such as water and foods, and some gases. Usually best applied when high accuracy is required at a reasonable price. PD meters represent 8% of global sales for flowmeters.
Differential pressure flowmeters use Bernoulli’s equation to measure the flow of fluid in a pipe. Differential pressure flowmeters introduce a constriction in the pipe that creates a pressure drop across the flowmeter. When the flow increases, more pressure drop is created. Impulse piping routes the upstream and downstream pressures of the flowmeter to the transmitter that measures the differential pressure to determine the fluid flow. This technology accounts for about 21% of the world market for flowmeters.
Bernoulli’s equation states that the pressure drop across the constriction is proportional to the square of the flow rate. Using this relationship, 10 percent of full scale flow produces only 1 percent of the full scale differential pressure. At 10 percent of full scale flow, the differential pressure flowmeter accuracy is dependent upon the transmitter being accurate over a 100:1 range of differential pressure. Differential pressure transmitter accuracy is typically degraded at low differential pressures in its range, so flowmeter accuracy can be similarly degraded. Therefore, this non-linear relationship can have a detrimental effect on the accuracy and turndown of differential pressure flowmeters. Remember that of interest is the accuracy of the flow measurement system — not the accuracy of the differential pressure transmitter.
Different geometries are used for different measurements, including the orifice plate, flow nozzle, laminar flow element, low-loss flow tube, segmental wedge, V-cone, and Venturi tube.