Best Technology Guide to Differential Pressure Flow Meters
Differential Pressure Flow Meters also called DP flow meters. Differential pressure flow meters consist of flow sensors and pressure/differential transmitters. DP Flow Meters measure the flow rate based on the differential pressure measured by the flow sensor parts. Flow sensors are the important part of differential pressure flow meters. Like: Orifice plate, Venturi tube, Wedge, V-cone and Averaging Pitot Tubes.
Differential pressure (DP) flow meters are suitable for applicaitons, like: water, gas, steam, oil….
Featured Differential Pressure Flow Meters
- What is a differential pressure flow meter ?
- Differential Pressure Flow Meters Types
- Advantages and disadvantages of differential pressure flow meter
- How Differential Pressure Flowmeters Work ?
- Differential Pressure Flow Meters Applications
- Application Cautions for Differential Pressure Flowmeters
- How to Use Differential Pressure Flowmeters
- How to calibrate a differential pressure flow meter ?
- Piping, Installation, & Maintenance
What is a differential pressure flow meter ?
Differential pressure flowmeter measures the flow rate by the static pressure difference. This static pressure difference is caused by the fluid flowing through the throttling device.
The most basic configuration of a differential pressure flow meter includes three parts:
a throttling device, a differential pressure signal line, and a differential pressure gauge.
There are many types of throttling devices. Such as: venturi, orifice plate, etc.
Yet, China’s metrology institutes have established national standards for orifice plates with angular contact pressure and flange pressure, and nozzles for angular contact pressure, which are called standard throttling devices.
Differential pressure flow meters have a wide range of applications.
All single-phase fluids can be measured. Including liquid, gas, steam, etc.
Can measure partial miscible flow. Such as gas-solid mixture, gas-liquid mixture, liquid-solid mixture, etc.
Differential pressure flowmeter products cover pipe diameters, working conditions (pressure and temperature) in general production processes. The most common application is the standard orifice plate flowmeter.
The standard orifice plate flowmeter structure is easy to replicate. Simple and sturdy. Stable and reliable performance. Long service life and low price. Standard type detection elements are recognized by the International Organization for Standardization and International Legal Metrology Organization, and can be put into use without actual flow calibration.
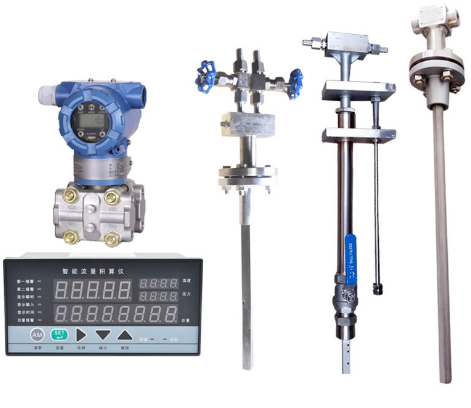
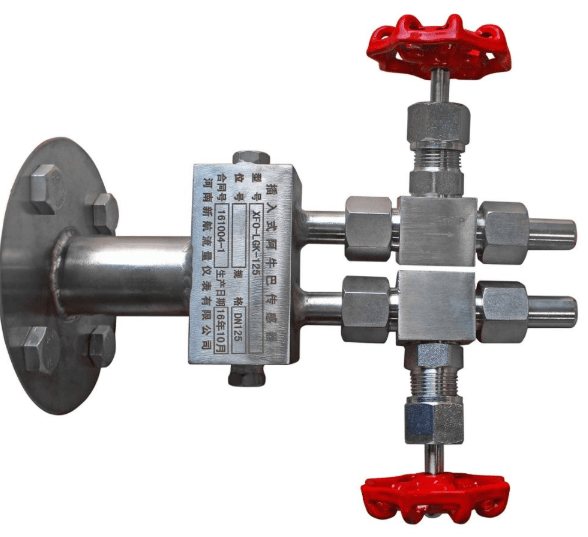
Differential Pressure Flow Meters Types
Primary Element | Recommended Service | Minimum RE Limits | Size | Advantages | Limitations |
Square edge concentric Orifice Plate | Clean liquids, gases, steam | ≥2000 | ≥1/2 in | Easy to install; Low Cost; Easy to replace | Relaxation piping requirements; High head loss; Accuracy affected by installation and orifice condition |
Conical/ quadrant edge concentric orifice plate | Viscous liquids | ≥500 | 1 to 6 in | Easy to install; Low Cost; Easy to replace | Relaxation piping requirements; High head loss; Accuracy affected by installation and orifice condition |
Eccentric/segmental orifice plate | Liquids and gases containing secondary fluid phases | >10,000 | 4 to 14 in | Easy to install; Low Cost; Easy to replace | Relaxation piping requirements; High head loss; Accuracy affected by installation and orifice condition; Higher uncertainties of discharge coefficient data |
Integral orifice | Clean liquids, gases, steam | >10,000 | 1/2 to 2 in | Easy to install; Low Cost; No lead lines; | Relaxation piping requirements; Proprietary design requires calibration; High head loss; More prone to clogging than standard orifice plate |
Venturi/flowtube | Clean & dirty liquids, gases, steam; slurries | >75,000 | 1/2 to 72 in | Low head loss; 2 to 9 times less relaxation piping than orifice; Higher flow capacity than orifice for the same differential pressure; Accuracy less affected by wear and installation conditions than orifice; | High initial cost |
Nozzle | Clean liquids, gases, steam | >50,000 | 2 in | Higher flow capacity than orifice for the same differential pressure; Accuracy less affected by wear and installation conditions than orifice; Good for high temperature and high velocity applications; Mass transfer standard for gases; | Harder to replace than orifice; High head loss; |
Segmental wedge | Dirty liquids, gases, steam; slurries; viscous liquids; | >500 | ≥1/2 in | No lead lines; Minimal clogging potential; 40% less head loss than orifice; Minimal relaxation piping; | Proprietary design needs calibration; High initail cost; Requires remote seal differential pressure transmitter, harder to zero; |
Venturi cone | Clean & dirty liquids, gases, steam; Viscous liquids | None cited | 1 to 16 in | Minimal relaxation piping; Low flow capability; | Proprietary design; |
Advantages and disadvantages of differential pressure flow meter
The upside of this technology is low cost. Multiple versions can be optimized for different fluids and goals, are approved for custody transfer (though it is being used less and less for this). It is a well-understood way to measure flow, and it can be paired up with temperature/pressure sensors, to provide mass flow for steam and other gasses.
Negatives are that rangeability is not good due to a non-linear differential pressure signal (laminar flow elements excepted). Accuracy is not the best and can deteriorate with wear and clogging.
Advantages of throttling differential pressure flowmeter (orifice flowmeter)
- The standard orifice plate structure of the throttle piece is easy to copy. Simple, firm, stable and reliable in performance, long in service life and low in price;
- The throttling application range is extremely wide. All single-phase fluids, including liquid, gas, and steam, can be measured. Some mixed-phase flows, such as gas-solid, gas-liquid, liquid-solid, etc. can also be applied. General production processes and pipe diameters. The working condition (pressure, temperature) has products;
- All accessories can be used by all manufacturers if it is an international standard and can be used without calibration.
Disadvantages of throttling differential pressure flowmeter (orifice flowmeter)
The repeatability and accuracy of the measurement are medium levels;
The range is narrow because the meter signal and the flow rate are squared, the general range can only reach 3:1 ~ 5:1;
The requirements for on-site installation conditions are relatively high. If a long straight pipe section is required, it is difficult to meet;
The pressure piping is a weak link, which is prone to leakage, blockage, freezing and signal distortion;
The pressure loss is large.
How Differential Pressure Flowmeters Work ?
Differential pressure flowmeters use Bernoulli’s equation to measure the flow of fluid.
Differential pressure flowmeters introduce a constriction in the pipe. This part creates a pressure drop across the flowmeter.
When the flow increases, more pressure drop is created.
Impulse piping routes the upstream and downstream pressures of the flowmeter to the transmitter.
The transmitter measures the differential pressure and indicate the fluid flow. This technology accounts for about 21% of the world market for flowmeters.
Bernoulli’s equation states that the pressure drop across the constriction is proportional to the square of the flow rate. Using this relationship, 10 percent of full scale flow produces only 1 percent of the full scale differential pressure.
At 10 percent of full scale flow, the differential pressure flowmeter accuracy is dependent upon the transmitter. And the transmitters being accurate over a 100:1 range of differential pressure. DP transmitter accuracy is typically degraded at low differential pressures in its range. So flowmeter accuracy can be similarly degraded. Therefore, this non-linear relationship can have a detrimental effect on the accuracy and turndown of differential pressure flowmeters. Remember that of interest is the accuracy of the flow measurement system. Not the accuracy of the differential pressure transmitter.
Different geometries are used for different measurements. Including the orifice plate, flow nozzle, laminar flow element, low-loss flow tube, segmental wedge, V-cone, and Venturi tube.
where
- points 1 and 2 lie on a streamline,
- the fluid has constant density,
- the flow is steady,
- and there is no friction.
Although these restrictions sound severe, the Bernoulli equation is very useful, partly because it is very simple to use.
And partly because it can give great insight into the balance between pressure, velocity, and elevation.
Differential pressure use Bernoulli’s equation to measure the flow of fluid in a pipe.
Differential pressure flowmeters introduce a constriction in the pipe,
that creates a pressure drop across the flowmeter.
When the flow increases, more pressure drop is created.
y+P(x)y =Q(x)y^n (equation)
is called a Bernoulli differential equation where n is any real number
The graph below shows the resulting pressure drop for water at 60 F,
over a range of flow rates for a 100-foot long pipe,
for both 4 inches and 6-inch schedule 40 piping.
The continuous fluid medium moves in the pipeline. When the flow medium passes through the preset throttling device in the pipeline, its flow bundle will form a partially reduced diameter state at the throttling device. As a result, the flow velocity of the fluid medium is increased, and the hydrostatic pressure is relatively reduced. This condition creates a pressure drop (differential pressure) upstream and downstream of the throttle (orifice). The larger the flow of the flowing medium is, the larger the pressure difference between the upstream and downstream of the throttling device will be.
So, the pressure difference of the throttling measurement device can be used to relatively measure the flow rate of the fluid flowing through the throttling device through a certain conversion. This is the basic principle of using the throttling device to specifically measure the continuous flow of medium in the pipeline.
Differential Pressure Flow Meters Applications
The flexibility of differential pressure flowmeters makes them suitable for extremely diverse industrial flow applications. Typical uses include:
- Oil and Gas: Wellhead monitoring, flare gas measurement, transmission pipelines;
- Water and Wastewater: Flow monitoring in treatment plants, lift stations, and distribution systems;
- Electricity: Feedwater, condensate, cooling water, steam flow, stack emissions;
- Chemicals and Petrochemicals: Production monitoring, mixing/batching, loading rack measurement;
- Papermaking: Digester flow, black liquor, steam flow, custody transfer;
- Food and Beverage: Batching, sanitary production lines, plant energy management;
- Pharmaceuticals: Clean process liquids, transfers, batching;
- Metals and Mining: Material flow, pneumatic conveying lines;
- Air conditioning and heating: Chilled water, hot water, steam, compressed air, ventilation balance;
And many more are not listed. When accuracy, reliability and economy are important, differential pressure meters can meet even the most demanding application needs.
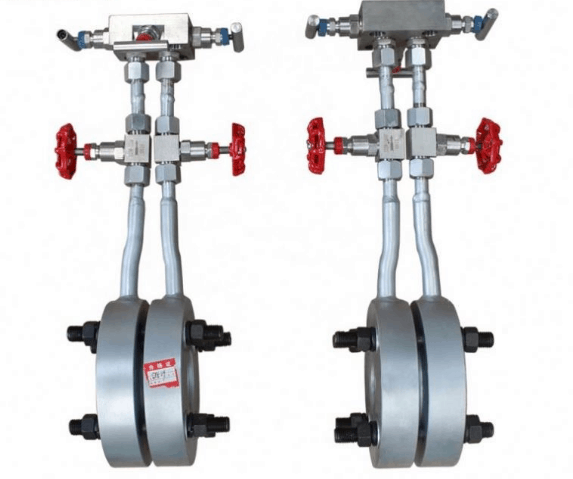
Application Cautions for Differential Pressure Flowmeters
- There is a non-liner relationship between flow and differential pressure. The accuracy of flow measurement in the lower portion of flow range can be degraded.
- Plugging of the impulse piping can be a concern for many services. For slurry service, purges should be used to keep the impulse piping from plugging.
- For liquid service, impulse piping should be oriented and sloped so that it remains full of liquid and does not collect gas.
- For gas service, impulse piping should be oriented and sloped so that it remains full of gas and does not collect liquids.
- In vapor service, vapor may be allowed to condense. In some of the impulse piping to form a liquid seal between the hot vapor and transmitter to protect the transmitter from heat.
- Be careful when you do the calibration of the differential pressure transmitter. Because the calibration can be affected by the accumulation of liquid or gas in the impulse tubing.
- Besides, the accuracy of the flow measurement system can be degraded. When varying amounts of liquid can accumulate during operation.
- Calibration issues can be important to the successful application of this DP flow technology. For example, differential pressure transmitter removal for calibration exposes the transmitter to multiple sources of potential problems. And this can affect the measurement. Not the least of which is the extent to which the transmitter tubing is retightened after calibration.
- Calibration should be performed in-situ when possible and provisions to do so should be addressed during the design phase. For example, the differential pressure transmitter can be purchased with an integral valve manifold. That allows easy calibration without disconnecting impulse tubing.
- Gas applications should be designed carefully. Because changes in operating pressure and operating temperature can dramatically affect the flow measurement. In other words, the gas density can vary significantly during operation. As a result, the differential pressure produced by the flowmeter can also vary significantly during operation. Failure to compensate for these effects can cause flow measurement errors of 20 percent or more in many applications.
- In these applications, a flow computer can be used to calculate the corrected flow measurement. Using actual pressure, temperature and flow measurements.
How to Use Differential Pressure Flowmeters
- Differential pressure flowmeters inferentially measure the flow of liquids, gases and vapor. Such as water, cryogenic liquids, chemicals, air, industrial gases, and steam. Be careful using differential pressure flowmeters for fluids with high viscosity. Such as some hydrocarbons and foods. Because their accuracy can be degraded when Reynolds number is low.
- This flowmeter can be applied to relatively clean fluids. Pay attention to materials of construction, the flow of corrosive fluids, such as found in the chemical industry, can be measured.
- Somewhat dirty fluids can be measured by purging the impulse piping with an inert fluid. Be careful when using differential pressure flowmeters in dirty services. Because the dirt can plug the impulse piping and cause incorrect measurements. Diaphragm seals can sometimes be applied in these applications. But one should remember that diaphragm seals can degrade the performance of the differential pressure transmitter system. And hence, the degrade the performance of the flow measurement system.
- Differential pressure flowmeters are generally applicable to many flows in most industries. Such as mining, mineral processing, pulp and paper, petroleum, chemical, petrochemical, water, and wastewater industries.
- Other flow measurement technologies may perform better than DP flowmeters in many applications. But differential pressure flowmeters are still used extensively due to long-standing user familiarity with the technology.
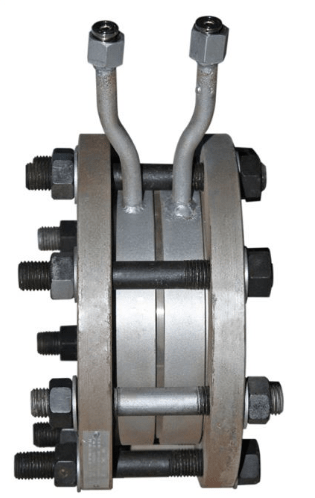
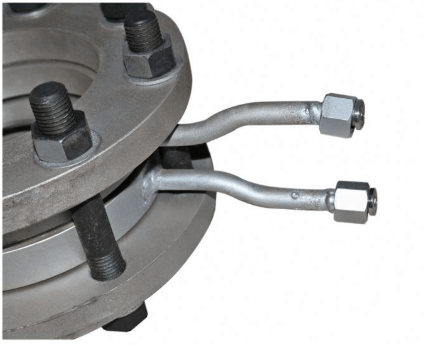
How to calibrate a differential pressure flow meter ?
Material
Data sheet
Pressure calibrator (std)
Multimeter (std)
Hart communicator
Example calculation
Instrument calibrated range: 0 – 2500 mmH2O
Process calibrated range: 0 – 105000 Nm3/h
Q =K P
0% 0 mmH2O = ( 0/2500) x 105000= 0 Nm3/h
50% 1250 mmH2O = ( 1250/2500) x 105000= 7424.6 Nm3/h
100% 2500 mmH2O = ( 2500/2500) x 105000 = 105000 Nm3/h
Step
WARNING – If the process is hazardous, please unsure proper flushing is done to remove the entire hazard.
- Ask panel man to put the controller in manual mode for control loop and to put it on MOS for ESD loop.
- Hook up HART Communicator and verify some parameters by refer to data sheet. Typical parameters are, tag number, PV, LRV and URV.
- Isolate the instrument from the process.
- Release both pressure and drain low and high side liquid throughout manifold drain.
- Connect pressure calibrator to high side of manifold
- Expose the low side to atmosphere
- Hook up a multimeter in series with the signal to the DCS to measure current signal.
- Apply pressure as per data sheet LRV (normally 0mmH2O)
- Multimeter should show 4mA
- If not, do zero adjustment at transmitter using HART Communicator
- Apply pressure as per data sheet URV
- Multimeter should show 20mA
- If not, do span adjustment at transmitter using HART Communicator
- Verify the linearity by increasing and decreasing the pressure (0%,25%,50%,75%,100%,75%,50%,25% and 0%of range)
- After completion of the job ask panel operator to put loops back in normal mode or normalize the MOS Fill the calibration form and file it for future reference.
Piping, Installation, & Maintenance
Installation of differential pressure flowmeters
- pipeline conditions;
- pipeline connection;
- pressure take-off structure;
- lengths of upstream and downstream straight pipe sections of the throttling device;
- and the laying of differential pressure signal pipelines.
1. Measuring tube. The measuring tube refers to the straight pipe section upstream and downstream of the throttle. The inner diameter D of the pipe used to calculate the diameter ratio of the throttling device. And D is the average value of the inner diameter within the upstream 0.5D length range of the upstream pressure taking port. The velocity distribution is different under turbulent flow. For the smooth and rough pipe in the inner surface of the straight pipe section is different. For newly installed pipes, pipes that meet the rough requirements should be selected. If the requirements are not met, measures such as coating or machining should be taken. After the instrument has been used for a long time, due to the characteristics of the measuring medium (corrosion, adhesion, scaling, etc.). The inner surface may change. It should be regularly inspected for cleaning and maintenance.
2. Throttling pieces. The verticality, coaxiality and connection with the measuring tube of the throttle element are strictly regulated. The throttle should be perpendicular to the pipe axis. The throttle should be coaxial with the pipe or clamp ring. The installation of the measuring tube before and after the throttle is apart from the throttle 2D. The measuring tube between the throttle and the first upstream choke can be composed of one or more sections of pipes with different cross sections.
3. Differential pressure signal pipeline. The differential pressure signal pipeline refers to the pressure-conducting pipeline of the throttling device and the differential pressure transmitter. Differential pressure flowmeters cause the most failures caused by the impulse. Such as blockage, corrosion, leakage, freezing, false signals. So, the installation of the differential pressure signal pipeline is very important.
Maintenance of differential pressure flowmeters
Differential pressure flowmeters need to do daily maintenance during the use.
- Before the production of the differential pressure flowmeter is put into operation. It should be strictly inspected by special personnel. Including line inspection, seal inspection, etc., to ensure that it is accurate before power can be supplied.
- Relevant responsible personnel should perform regular cleaning and lubrication work on the flowmeter. And if necessary, recalibrate the flowmeter to ensure the accurate operation of the flowmeter. When using lubricating oil, follow the instructions.
- Refueling operation should be carried out before the DP flowmeter is officially started. And at the same time, the refueling amount should be accurately controlled, which usually reaches the center of the sight glass.
- Lubricating oil is an important substance in differential pressure flow meters. If the lubricating oil in the sight glass is found to be black or 2mm higher than the center of the sight glass. It should be judged that the lubricant is deteriorated and should be replaced in time.
- Record and analyze the values recorded by the instrument in a timely manner to determine whether the flowmeter’s response to parameters such as density, temperature, and flow rate is accurate. If a problem occurs, handle it in a timely manner.
- Strictly maintain the normality of the filter. If problems are found and dealt with in a timely manner, you can judge by the value of the entrance and exit.
- For special application flow meters, such as those used in trade settlement, certain requirements should be made on the qualification of the test to ensure the accuracy of the data.
Common faults of differential pressure flowmeters
1: No output signal after installation;
Check the reasons:
(1) the power may not be supplied.
(2) the power and signal wires are connected correctly. And the instrument operator’s wrong operation caused the isolation liquid or condensate to be washed away.
2: The output signal is zero;
Check the reasons:
(1) whether the root-side shut-off valve on the positive and negative pressure side is open.
(2) whether the balance valve is closed, and check whether the positive-pressure side valve, the sewage valve. And the pressure guiding pipe are leaking.
3: The output signal is full scale;
Check the reason:
Check the flow for overload and reduce the flow.
Whether the negative pressure cut-off valve is open.
Open the cut-off valve. If the negative pressure side valve, blowdown valve, and pressure guiding tube leak, repair or replace it at the leak point.
4: The output value does not match the flow value;
Check the reason:
The filling of the isolation fluid is uneven or lost, refill.
The condensate level is inconsistent or the condensate is lost.
If the orifice plate is bent, replace the orifice plate.
If the surface of the throttle is dirty or rough, it must be cleaned.
5: The indicated value is too high
Check the reasons:
(1) Check whether the valve and pipeline on the negative pressure side are leaking. Close the valve in time to deal with the leak.
(2) There is gas on the negative pressure side, or the point of the positive pressure line is higher than the negative pressure line, which causes additional errors. Rearrange the line and discharge the gas in the negative pressure pipe.
(3) The negative pressure side pipeline is blocked, close the valve to clear the pipeline
(4) Negative pressure side shut-off valves are not fully opened, open in time
6: The indicated value is too low
Reason for inspection:
(1) The balance valve is not closed tightly, and it is closed promptly
(2) There are leakage points on the balance valve and the pipeline on the positive pressure side, and they must be repaired or replaced in time.
(3) There is gas on the positive pressure side, or the pipeline on the positive pressure side is lower than that on the negative pressure line, causing additional errors
(4) The positive pressure side shut-off valves are not fully opened. Open the shut-off valves in time.
(5) The right-angled edge of the orifice entrance becomes dull and seriously damaged, so it should be processed or replaced with a new orifice in time.
Sino-Inst manufactures flow meter as per customer’s flow measurement pressure. Different flow meters can bear differentia Mas pressure.
Usually, High pressure flow meters refer to high pressure turbine flow meters.
Diameter | DN200~DN3000mm |
Accuracy | 0.5% to 2.0% of reading |
Temp. range | -20~+150℃ |
Pressure | 40 MPa |
Flow rate | 0.5~6m/s |
Straight pipe required | Up stream≥5DN, down stream≥3DN |
Generally, we use mass flow meters to measure low pressure and low flow rates.
Diameter | DN10~DN6000mm |
Accuracy | ±1% |
Temp. range | -10~350℃ |
Pressure | Medium pressure≤10MPa |
Flow rate | 0.5-100m/s |
Protection | IP67 (sensor part) |