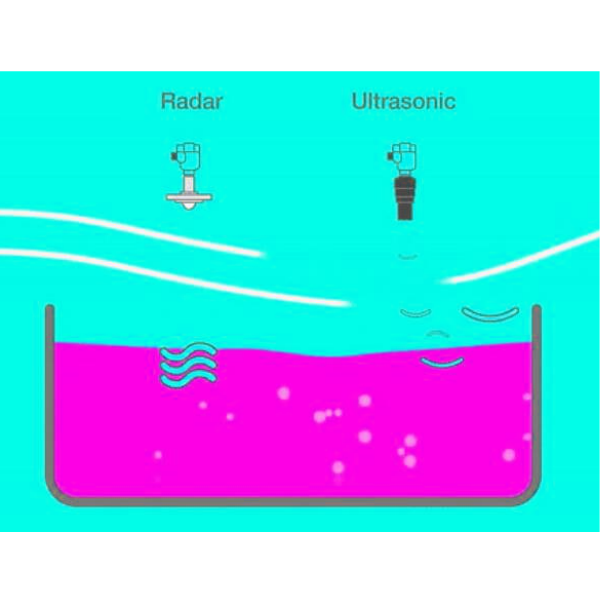
The biggest difference between radar and ultrasonic level transmitter is the different measurement principles. Ultrasonic level transmitter uses sound waves, and radar level meter uses electromagnetic waves. Different measurement principles lead to different application scenarios.
Radar and ultrasonic level transmitters are both non-contact level measurement technologies. Both types of liquid level meters send signals to the medium, and the signals are reflected by the medium and then return to the instrument. Distance is measured by calculating the time difference.
Featured Radar and Ultrasonic Level Transmitters
1. Different measurement principles
Ultrasonic Level Transmitter uses sound waves, while radar uses electromagnetic waves. This is the biggest difference between the two.
Ultrasonic Level Transmitter:
When the Ultrasonic Level Transmitter works, high-frequency pulse sound waves are emitted by the transducer (probe). When they encounter the surface of the object to be measured (water surface), they are reflected. The refracted reflection echo is received by the same transducer (probe) and converted into an electrical signal.
The time between pulse transmission and reception (the movement time of the sound wave) is proportional to the distance from the transducer to the object surface. The relationship between the distance S of sound wave transmission, the speed of sound C and the transmission time T can be expressed by the formula: S= CⅩT /2
Radar Level Meter:
Transmission-reflection-reception is the basic working principle of Radar Level Meter. The antenna of the radar sensor emits electromagnetic wave signals in the form of a beam, and the emitted waves are reflected on the surface of the material being measured. The reflected echo signals are still received by the antenna.
Each point in the transmitted and reflected beams is collected using ultrasonic sampling. After the signal is processed by the intelligent processor, the distance between the medium and the probe is obtained and sent to the terminal display for display, alarm, operation, etc.
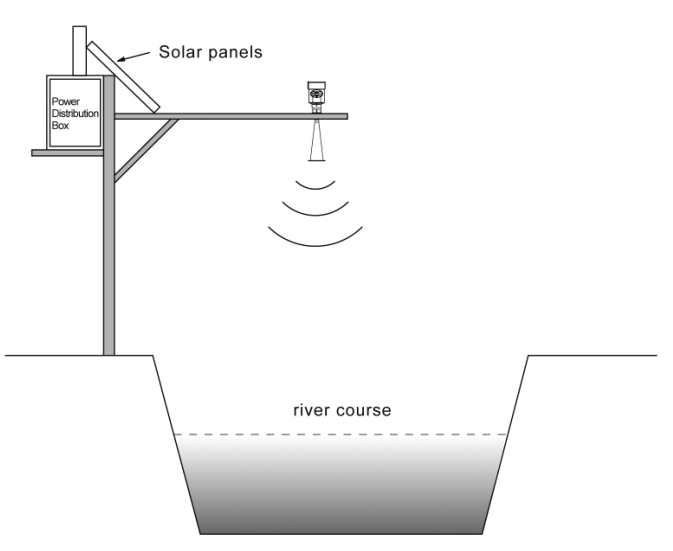
2. The measurement blind spots are different.
Dead zones must be considered when installing Ultrasonic Level Transmitter. When the liquid level enters the blind zone, the ultrasonic transmitter cannot measure the liquid level. Therefore, when determining the measuring range of the ultrasonic level meter, it is recommended to leave a margin of 50 cm.
During installation, the transmitter probe must be about 50 cm higher than the maximum liquid level. Only in this way can the accurate monitoring of the liquid level and the safety of the ultrasonic liquid level meter be ensured.
The blind zone of the radar level meter will be smaller. For example, the Blind zone of Sino-Inst’s 80G high-frequency radar level meter can be 0.1m/0.2m/0.3m.
3. Different application situations
Due to the different measurement principles of ultrasonic and radar, their application scenarios are also different.
Radar level meters use electromagnetic waves, which are affected by the dielectric constant of the material being measured. Ultrasonic waves are mechanical waves, which are affected by the density of the medium being measured.
Therefore, when measuring substances with very low dielectric constants, the measurement effect of radar level meters will be greatly reduced.
Ultrasonic waves are sound waves and mechanical waves that need to be propagated through a propagation medium. Therefore, the Ultrasonic Level Transmitter cannot be used in working conditions such as vacuum, excessive steam content, or foam on the liquid surface.
Radar liquid level meters are available in horn type, rod type, and cable type, and can be used in different measuring industries. Therefore, compared with Ultrasonic Level Transmitter, radar level meter can be applied to more complex working conditions.
4. Different temperature and pressure tolerances
Ultrasonic Level Transmitter has temperature limits. Generally, the temperature at the probe cannot exceed 80 degrees, and the speed of sound waves is greatly affected by temperature.
Ultrasonic Level Transmitter is greatly affected by pressure and is generally required to be within 0.3MPa. Because sound waves are emitted by vibration, the sound-producing components will be affected when the pressure is too high.
Ultrasonic Level Transmitter cannot measure well when there is a lot of fog or dust in the measurement environment.
In contrast, radar uses electromagnetic waves and is not affected by vacuum. The applicable range of medium temperature and pressure is very wide. With the emergence of high-frequency radar, its application scope has become wider. 200℃, 400℃ high temperature, 2.5MPa high pressure, etc. can be customized.
5. Different accuracy:
The accuracy of radar level meter is higher than Ultrasonic Level Transmitter.
The accuracy of radar is definitely higher than ultrasonic. Millimeter-wave radar, with a measurement accuracy of up to ±1mm.
The accuracy of Ultrasonic Level Transmitter is around 0.3%~0.5%.
6. Costs vary
In terms of price, compared with Ultrasonic Level Transmitter, the price of radar level meter will be higher.
More Level Measurement Solutions
- Industrial Ultrasonic Level Transmitters | Non-contact Level Measurement
- Featured 5 Guided Wave Radar Level Transmitter Types
- Guided Wave Radar Level Transmitter Installation Guide and Troubleshooting
- Difference Between Radar and Guided Wave Radar Level Transmitter
- Hydrostatic Level Measurement-Liquid Level Measurement with Pressure Sensors
- Tank Level Measurement with Pressure Transmitters/DP Transmitters
The measurement principle of radar and ultrasonic level transmitter is to send a signal to the medium, and then the signal is reflected by the medium and then returns to the instrument. The distance is measured by calculating the time difference.
Difference between radar and ultrasonic level transmitter: Ultrasonic waves rely on air to propagate. Therefore, all factors that can affect the air will affect ultrasonic waves. Radar is an electromagnetic wave. Compared with mechanical waves such as ultrasonic waves, it is not affected by the environment.
Both radar level meter and ultrasonic level transmitter can be used well for liquid level measurement. However, the specific choice of level meter in actual applications should be determined based on process conditions, medium characteristics, installation conditions, usage environment and other factors.
If you need non-contact liquid level measurement or have related technical questions, please contact our engineers!