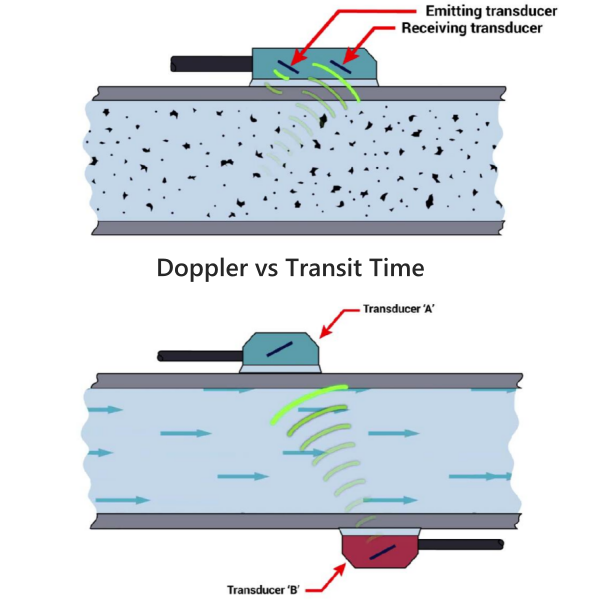
Ultrasonic flow meters use ultrasonic technology to measure liquid flow. There are two main types: Doppler effect and transit time. Both Doppler Effect and Transit Time ultrasonic flowmeters can be equipped with external clamp or insert sensors. Suitable for measuring large pipe diameters and fluids that are not easily accessible.
Doppler Effect and Transit Time flow meters work similarly, but the technology is very different. Understand the principles and advantages of them and choose a more suitable flow meter for your application. Get more accurate measurements.
What is a Doppler Ultrasonic Flow Meter?
Doppler flowmeter is a type of ultrasonic flowmeter that uses the Doppler effect principle to measure the velocity of fluid. Discontinuities in any flowing liquid will cause a frequency shift in the reflected ultrasonic signal (that is, a phase difference in the signal). By measuring the phase difference, the flow rate can be measured. The technology is widely used in a variety of industrial applications, including chemical processing, water treatment, and oil and gas production, due to its accuracy, non-invasiveness and versatility.
Theoretically, these discontinuities could be suspended bubbles, solids, or interfaces caused by fluid disturbances. The sensor generates and receives ultrasonic signals and provides data to the host. The host processes the signals and provides analog outputs for speed display, volume flow display and accumulation, and relay output.
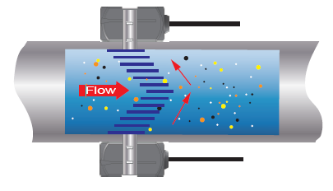
Fluid velocity can be calculated as
v = c (fr – ft) / (2 ft cosΦ)
where
fr = received frequency
ft = transmission frequency
v = fluid flow velocity
Φ = relative angle between the ultra transmittedsonic beam and the fluid flow
c = velocity of sound in the fluid
This method requires there is some reflecting particles in the fluid. The method is not suitable for clear liquids.
What is a Transit Time Ultrasonic Flow Meter?
Transit Time Ultrasonic Flow Meter measures the time difference from when an ultrasonic signal is transmitted from the first sensor to when it travels through the pipe and is received by the second sensor. Kanto flow rate is calculated based on the time difference.
If there is no flow, the travel time will be the same in both directions.
When there is flow, sound travels faster if it travels in the same direction; as the fluid moves faster, the difference between upstream and downstream times increases. The transmitter processes upstream and downstream times to determine flow.
If traveling in the opposite direction, sound travels more slowly.
Because the ultrasonic signal must pass through the pipe to be received by the sensor, the liquid cannot contain large amounts of solids or air bubbles, otherwise the high-frequency sound will be attenuated and too weak to pass through the pipe.

When the ultrasonic beam propagates in a liquid, the flow of the liquid will cause a small change in the propagation time. And the change in the propagation time is proportional to the flow velocity of the liquid. The relationship is as follows:
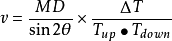
Where:
θ is the angle between the sound beam and the direction of liquid flow.
M is the number of linear propagations of the sound beam in the liquid.
D is the inner diameter of the pipe.
Tup is the propagation time of the sound beam in the positive direction.
Tdown is the propagation time of the sound beam in the reverse direction.
ΔT = Tup –Tdown
Let the speed of sound in a stationary fluid be c. The velocity of the fluid flow be u. And the propagation distance be L.
When the sound wave is in the same direction as the fluid flow (that is, in the downstream direction), its propagation velocity is c + u. Otherwise, the propagation velocity is cu.
Place two sets of ultrasonic generators and receivers (T1, R1) and (T2, R2) at two places separated by L.
When T1 transmits ultrasonic waves in the forward direction and T2 in the reverse direction.
The time required for the ultrasonic waves to reach the receivers R1 and R2 is t1 and t2, then:
t1 = L / (c + u); t2 = L / (c-u)
Because in industrial pipelines, the velocity of the fluid is much smaller than the speed of sound, that is, c >> u, the time difference between the two is ▽ t = t2-t1 = 2Lu / cc.
It can be seen that when the sound wave propagates in the fluid c When known, the flow velocity u can be obtained by measuring the time difference ▽ t, and the flow rate Q can be obtained.
Featured Ultrasonic Flow Meters
Differences: Doppler Effect vs Transit Time
Differences in working principles
As stated above, Doppler flow meters are based on Doppler effect measurements. Utilizes the Doppler frequency shift phenomenon produced by sound waves. Measurements are made by calculating the scatterer flow velocity by detecting the Doppler shift produced by acoustic waves emitted from a moving source at a stationary point. The Doppler method flowmeter is suitable for measuring turbid fluids, but it can only measure fluids with impurities above about 50mg/L. The measurement accuracy of the Doppler method is lower than that of the transit time method.
The time difference method of ultrasonic flowmeter indirectly measures the fluid flow rate by measuring the time difference between the downstream and countercurrent propagation of ultrasonic signals in the fluid, that is, the time difference. The fluid flow rate can then be calculated from the flow rate. The transit time method is suitable for measuring pure fluids. Fluids with more bubbles or impurities will hinder the normal propagation of ultrasonic waves and cause inaccurate measurement results.
Differences in applications
Because Doppler flow meters rely on the detection of bubbles or solid particles. Therefore, it is suitable for situations where there are many bubbles or particles in the fluid. Such as sewage treatment, petrochemical, cement and other industries.
The transit-time ultrasonic flowmeter is suitable for situations where there are few bubbles or solid particles in the liquid. Such as tap water, beverage, pharmaceutical and other industries.
Differences in accuracy and measurement range
The measurement accuracy of Doppler flowmeter is mainly affected by factors such as the placement position of the probe and the consistency of the fluid. Generally, the accuracy is low. At 0.5FS~2%FS.
The measurement accuracy of the time difference ultrasonic flowmeter is higher, up to 1%. And it can measure a wide range of flow rates, including low speed and high speed.
Differences in structure and price
The structure of Doppler flowmeter is complex and its price is higher than that of ultrasonic flowmeter. The time-lag ultrasonic flowmeter has a simple structure, is easy to install, and is relatively cheap.
To sum up, there are certain differences between Doppler flowmeters and transit-time ultrasonic flowmeters in terms of working principles, applicable occasions, accuracy and measurement range, structure and price. A suitable flow meter should be selected based on actual needs.
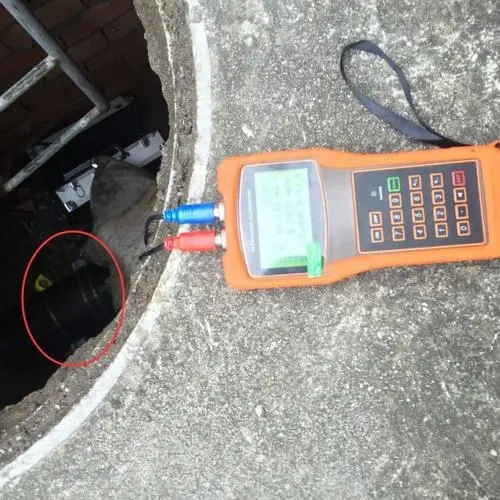
More Flow Measurement Solutions
- Doppler Effect Ultrasonic Flow Meters | Sino-Inst
- Top Explosion Proof Flow Meters for Explosive or Hazardous Areas
- Hydrogen Flow Meters for Mass and Volume Flow
- Beverage Flow Meters for Flow Monitoring and Quantitative Filling
- Industrial Digital Helium Flow Meters | Mass-Volume Flow
- Liquid and Gas NH3 Ammonia Flow Meters
- Magnetic Flow Meter Lining Material and Electrode Selection Guide
- Electronic Flow Meters-Digital Display
Ultrasonic flowmeter is a flow meter that has been used since the 1970s. Like electromagnetic flowmeter, because there are no obstructions in the flow channel of the meter, it is an unimpeded flowmeter. It is suitable for measuring large pipe diameters and fluids that are not easily accessible.
Ultrasonic flow meter measurement is an indirect measurement method, mainly including Doppler method and time difference method. Doppler ultrasonic flowmeter is widely used in sewage measurement. A single pure fluid is more suitable for transit time ultrasonic flowmeter.
Sino-Inst supplies various types of Doppler Effect and Transit Time ultrasonic flow meters. If you need to purchase or have related technical questions, please contact our engineers!