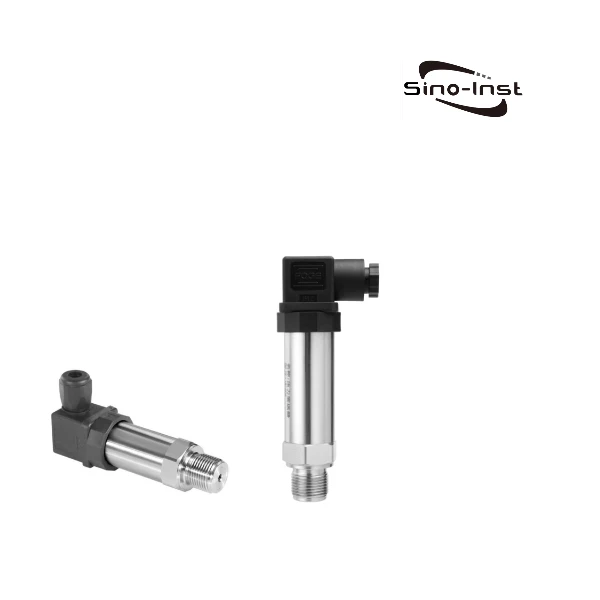
Intelligent Pressure Sensor is also called Intelligent Pressure Transducer.
SI-1185 Intelligent Pressure Sensor converts the pressure signal of the measured medium into a 4~20mADC standard signal or superimposes a HART digital signal or RS485 signal. Realize remote control. Support fieldbus-based field control technology upgrades. Integrated structural design and standardization Signal output, small size, high precision, light weight, wide range coverage. It is suitable for places in various industries that require precise measurement of fluid pressure or liquid level.
Features of Intelligent Pressure Sensor
- High precision, using digital compensation and nonlinear correction technology.
- Pressure type optional: gauge pressure, absolute pressure, negative pressure
- -10℃~80℃ digital temperature compensation without breakpoint, strong anti-electromagnetic compatibility ability
- Small size, high stability, high sensitivity, high cost performance
- A variety of process connections and electrical connections can be customized according to customer requirements
- Optional digital communication function, RS485 communication or HART communication protocol
- Support networking applications
SI-1185 Intelligent Pressure Sensor Specifications
Measuring medium: | Various liquids, gases and vapors compatible with 304, 316L stainless steel |
Range: | 0-0.1…100MPa |
Overload: | 1.5 times full scale pressure |
Pressure type: | Gauge or absolute or sealed gauge |
Accuracy: | ±0.2%FS; ±0.5%FS |
Long-term stability: | ±0.2%FS/year |
Zero temperature coefficient: | ±0.03%FS/°C (reference 25°C) |
Full scale temperature coefficient: | ±0.03%FS/°C (reference 25°C) |
Compensation temperature: | -10~80℃ |
Medium temperature: | -35~85℃, -35~200℃, high temperature is greater than 200 degrees can be customized according to customer requirements, the actual temperature range of the product measurement medium please Refer to the temperature range printed on the product nameplate. |
Operating temperature: | -30~85℃ |
Storage temperature: | -40~120℃ |
Power supply: | 24VDC (12~28V) |
Output signal: | 4-20mA; 0-5VDC; 0-10VDC; 4-20mA+HART; RS485, customer optional |
Load capacity: | ≤(U-10)/0.20Ω; RS485 bus can connect 99 transmitters |
Insulation resistance: | 100MΩ,500VDC |
Shell protection: | IP65 |
Vibration: | 20g(20~5000Hz) |
Shock: | 20g(11ms) |
Order Guide
SI-1185 | Intelligent Pressure Sensor | ||
Code | Range | ||
(0~X)KPa | 0-0.1…100MPa | ||
Code | Output Signal | ||
B1 | 4-20mA | ||
B7 | RS485 | ||
B8 | HART | ||
Code | Process Connection | ||
P1 | M20*1.5 | ||
P3 | G1/4 | ||
P4 | G1/2 | ||
Code | Electrical connections | ||
C1 | Hirschman joint | ||
C2 | cable output | ||
C3 | Aviation Connector | ||
Code | Structural materials | ||
Diaphragm | interface | shell | |
M1 | 316L | 316L | SS |
M2 | 316L | 316L | 316L |
M3 | Tantalum | Hastelloy C | 316L |
M4 | titanium | titanium | 316L |
Code | Additional functions | ||
G | Gauge pressure (default) | ||
A | Absolute pressure | ||
S | Sealed gauge pressure | ||
v | Viton O-ring (default) | ||
j | Nitrile O-ring | ||
W | Waterproof and breathable treatment | ||
SI-1185 (0-1)MPa B1B7 P1 C1 M1 Gv |
Intelligent Pressure Sensor Applications
- Hydraulic and pneumatic control system
- Liquid level measurement and control, building automation, constant pressure water supply
- Petrochemical, environmental protection, energy, machinery and equipment industries
- Ships, utility vehicles and mobile hydraulic equipment
- Laboratory, industrial process detection and control
- Equipment automation, automatic control and detection system
- The urban pipe network, oil field pipeline, and pressure network of large and small hydropower stations form a twisted pair network through the RS485 bus, which is especially suitable for computer control systems;
Frequently
Asked
Questions
More Featured Pressure Sensors
Sino-Inst is a manufacturer of Intelligent Pressure Sensors. We supply more than 20 types of Intelligent Pressure Sensors.
There are many types of pressure sensors, such as resistance strain gauge pressure sensors, semiconductor strain gauge pressure sensors, Silicon piezoresistive pressure sensors, inductive pressure sensors, capacitive pressure sensors, resonant pressure sensors and capacitive sensors.
The Intelligent Pressure Sensors adopts high-precision and high-stability chip assembly of imported stainless steel isolation diaphragms. The product is manufactured through precise structural design, reasonable temperature compensation, linear processing circuit, V/I converted and steel seding fully shell.
SI-1185 Intelligent Pressure Sensors output signal 4~20mA, 0~10mA, 0~5VDC, etc. RS485 interface/HART protocol optional. The product can be used to measure the pressure of high temperature gas, liquid and steam and the pressure of corrosive medium. According to needs, it can be equipped with a linear 100% pointer gauge or a digital display gauge.
Sino-Inst has provided pressure measurement solutions to customers for many years. Our pressure sensor, made in China. Widely exported to the United States, Britain, Germany, South Africa, Norway and other countries.
If you need SI-1185 Intelligent Pressure Sensors, but have technical questions, please feel free to contact our sales engineers.