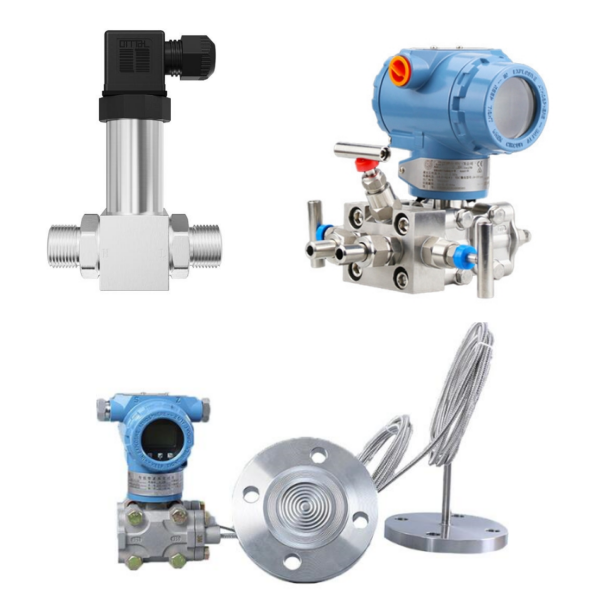
Differential pressure transmitters are transmitters that measure the difference in pressure across the transmitter. Output standard signals (such as 4~20mA, 0~5V).
Differential pressure transmitters are mainly used to measure differential pressure, pressure and negative pressure of liquids, gases and steam. It is also possible to measure liquid levels in open or pressurized vessels. Equipped with a throttling device, it can measure the flow of liquid, gas or steam, and convert the measured parameters into a 4-20mA DC signal output. Density can also be measured with a differential pressure transmitter.
Featured Industrial Differential Pressure Transmitters
differential pressure transmitter working principle
A differential pressure transmitter is a transmitter that measures the difference in pressure at both ends of the transmitter and outputs a standard signal (such as 4~20mA, 0~5V). Differential pressure transmitters are different from ordinary pressure transmitters in that they have two pressure interfaces.
Differential pressure transmitters are generally divided into positive pressure end and negative pressure end. Generally, the pressure at the positive pressure end of the differential pressure transmitter should be greater than the pressure at the negative pressure section before measurement can be made.
The differential pressure from the pressure-conducting pipes on both sides acts directly on the isolation diaphragms on both sides of the transmitter sensor. The sealing liquid in the diaphragm is conducted to the measuring element.
The measuring element converts the measured differential pressure signal into a corresponding electrical signal and passes it to the converter. After amplification and other processing, it becomes a standard electrical signal output.
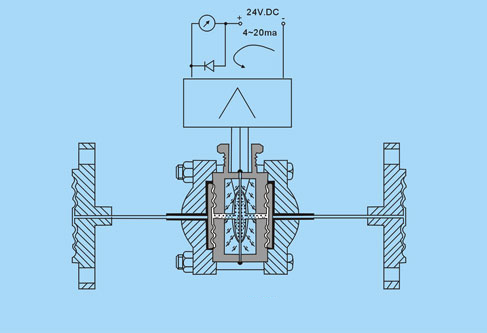
Types of differential pressure transmitters
Capacitive Differential Pressure Transmitter
This transmitter uses a capacitive sensor. The process pressure passes through isolating diaphragms on both sides or on one side. Then the filling fluid acts on the tensioned measuring diaphragm in the delta element (ie, the sensitive element). The measuring diaphragm and the capacitive plates on the insulators on both sides each form a capacitor.
When the pressure on both sides is inconsistent, the measuring diaphragm will be displaced. Its displacement is proportional to the pressure difference. This displacement is converted into differential capacitance formed on the capacitor plates. The differential capacitance is converted into a 4-20mADC two-wire current signal by an electronic circuit.
Diffused silicon differential pressure transmitter
The diffused silicon differential pressure transmitter uses diffused silicon sensing technology. By applying the measured pressure to the silicon chips on both sides respectively, the tiny resistance changes inside the silicon chip are converted into electrical signal output.
Differential pressure transmitters also include measures such as temperature compensation and linear correction to ensure the accuracy and stability of the output signal.
Monocrystalline silicon differential pressure transmitter
The sensor used in the monocrystalline silicon differential pressure transmitter utilizes the piezoresistive effect of monocrystalline silicon.
When single crystal silicon material is subjected to axial stress, its resistivity will change. This phenomenon is called the piezoresistive effect.
Taking advantage of this phenomenon, four mutually symmetrical strain resistors were produced on a single crystal silicon wafer using photolithography and etching processes. Form a Wheatstone bridge.
When the monocrystalline silicon wafer senses pressure changes, the resistance of the two pairs of arms of the bridge changes. causing the bridge output voltage to change. Thus achieving pressure to voltage conversion.
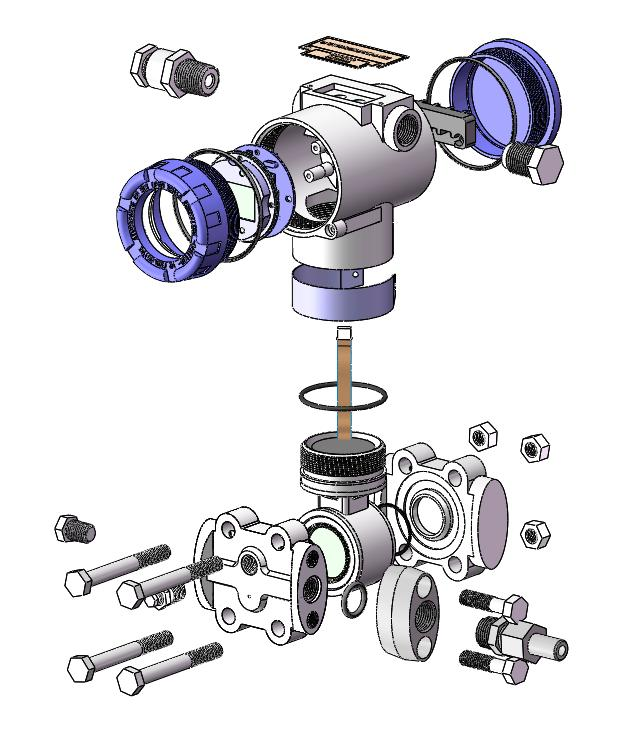
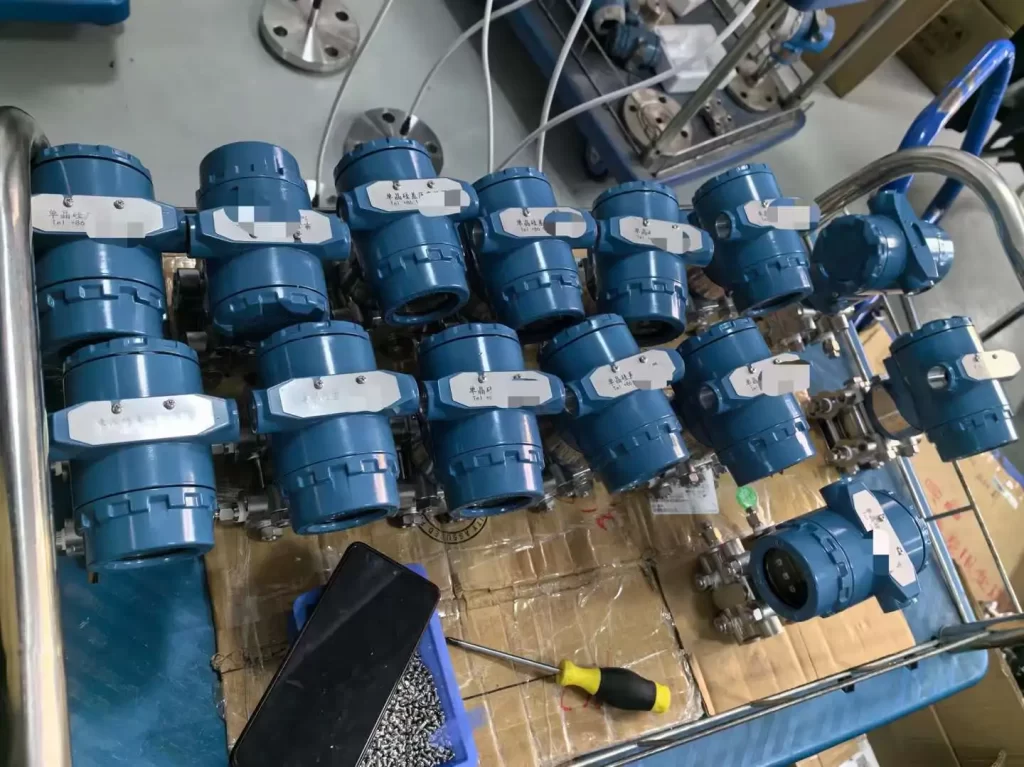
Differential Pressure Transmitter Industrial Applications
Differential pressure transmitters are widely used in petroleum, chemical, electric power, metallurgy and other industries. This product is mainly used to measure differential pressure, pressure and negative pressure of liquids, gases and steam. It is also possible to measure liquid levels in open or pressurized vessels. Equipped with a throttling device, the flow rate of liquid, gas or steam can be measured. And convert the measured parameters into 4~20mA DC signal output. And passed to the secondary instrument or regulating unit for detection or control.
Measure pressure
The differential pressure transmitter has two pressure holes. Just plug one of them up. It can be used to measure pressure.
Measure differential pressure
Connect the pressure source to the high pressure and low pressure pressure holes of the differential pressure transmitter. You can measure differential pressure.
Measure liquid level
Pressure transmitters and differential pressure transmitters can be used to measure the level of liquids such as water or fuel in vented or sealed tanks. And in many special working conditions, it has advantages that other liquid level transmitters cannot match. For example, measurement of viscos , high-temperature, corrosive liquids or gases in vacuum tanks.
Read More about: Tank Level Measurement with Pressure Transmitters/DP Transmitters
Measure flow
The differential pressure generated by the throttling member is used to measure the pipeline flow. This is our differential pressure flow meter.
Differential Pressure Flow Meters, also called DP flow meters. Differential pressure flow meters consist of flow sensors and pressure/differential transmitters. Flow sensors are the important part of differential pressure flow meters. Like: Orifice plate, Venturi tube, Wedge, V-cone and Averaging Pitot Tubes.
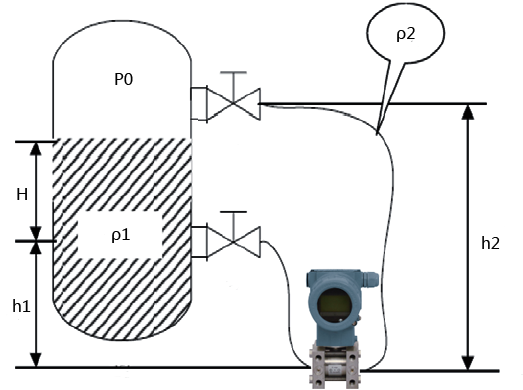
Read more about: Differential Pressure Flow Meter Technology
Measure density
The principle of the differential pressure density meter can calculate the density value based on the differential pressure value of the medium at a certain vertical distance. It can also automatically perform temperature compensation, with high accuracy, good reliability, and simple installation and use.
It is a two-wire density transmitter. It is mainly used for industrial process control.
The online density meter generates a corresponding 4-20mA signal according to the concentration and density, and can be remotely calibrated and monitored through digital communication.
More Pressure Measurement Solutions
- DP Transmitters for Filter Differential Pressure Monitoring
- 4 Wire – 3 Wire – 2 Wire Ultrasonic Level Transmitter
- 2 Wire-3 Wire-4 Wire Pressure Transducer Wiring Diagram
- Industrial Analog Pressure Transducers | 4-20mA, 0-5/10V DC
- Submersible Pressure Transducers for Liquid Pressure and Level Measurement
- Explosion Proof Pressure Transducers- Intrinsically Safe – ExdIICT6-ExiaIICT6 Ga
- Liquid Level Controllers and Switches for Industrial Tanks
- Voltage Output Pressure Transducers | 0-5/10V DC, 1~5VDC, 0.5~2.5VDC
- Industrial Hydrogen Pressure Transmitters/Transducers
The differential pressure transmitter measures the pressure difference of the medium in the process pipeline or tank. It converts the measured differential pressure value into a current signal output through data conversion and square root.
When choosing a differential pressure transmitter, we need to consider the differential pressure value, medium, working pressure, working temperature, and signal output, etc.
If you need to purchase a differential pressure transmitter or have related technical questions, please contact our engineers!