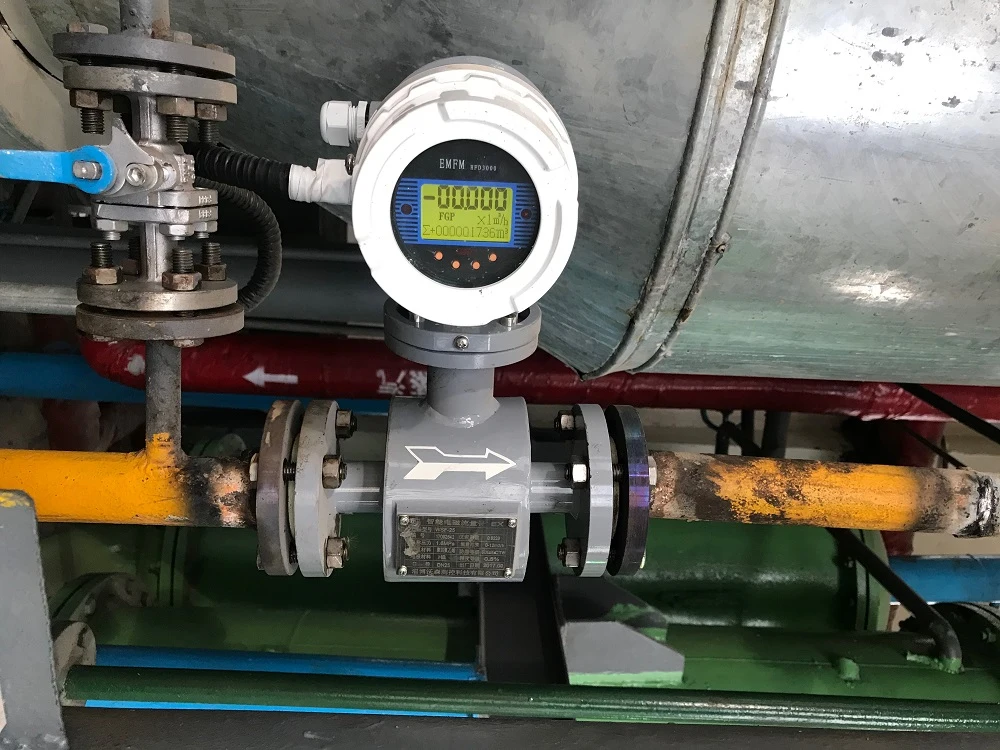
One of the bear-sized challenges in flow measurement is electromagnetic interference (EMI), which can misrepresent readings, compromise accuracy, and lead to costly functional inefficiencies.
To extenuate this issue, engineers have developed electromagnetic interference resistant flow meters—specialized instruments designed to operate reliably even in environments with high EMI.
This article explores the causes of EMI, the working principles of EMI-resistant flow meters, key features, applications, and best practices for installation and maintenance.
What is EMI?
Electromagnetic Interference (EMI) is the interruption of operation of an electronic device when it is in the neighborhood of an electromagnetic field in the radio frequency (RF) spectrum.
Many an electronic devices go wrong to work properly in the presence of strong RF fields. The disruption may interrupt, obstruct, or otherwise put down or limit the impelling performance of the circuit. The source may be any object, artificial or natural, that carries speedily changing electrical currents.
Root of EMI in Industrial Environments
- High-power electrical equipment (motors, generators, transformers)
- Variable frequency drives (VFDs) used in automation
- Radio frequency (RF) transmissions from communication devices
- Arc welding, plasma cutting, and other manufacturing processes
- Nearby power lines and substations
In such environments, standard flow meters may struggle to provide accurate readings due to EMI-induced signal corruption.
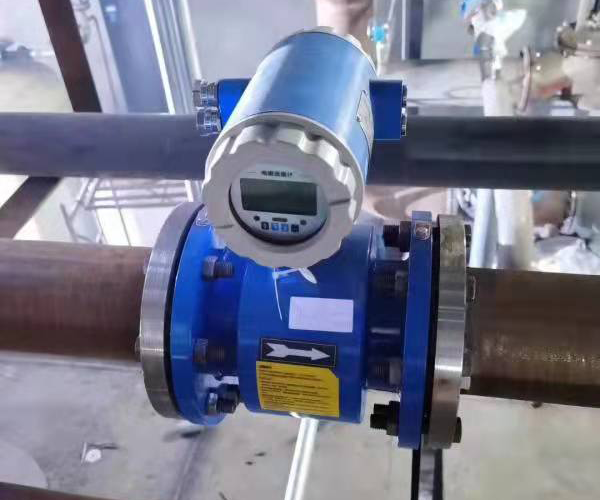
How EMI-Resistant Flow Meters Work?
EMI-resistant flow meters are designed with advanced technologies that shield them from electromagnetic disturbances. These meters incorporate the following features:
- Shielded Electronics and Circuitry
The internal electronic components are housed in Faraday cages or shielded enclosures to block external EMI.
Printed circuit boards (PCBs) are designed with grounding and noise-filtering techniques to reduce signal interference.
- Differential Signal Processing
Many modern flow meters use differential signal processing, where two signals are measured simultaneously. By comparing these signals, the system can distinguish real flow data from noise-induced fluctuations.
- Robust Grounding and Isolation
Proper grounding prevents unwanted currents from affecting the sensor and electronics.
Optical isolation is often employed to separate the flow meter’s power and signal transmission from noisy environments.
- Advanced Filtering Algorithms
Digital signal processing (DSP) techniques are used to filter out high-frequency noise without affecting measurement accuracy.
Adaptive algorithms can distinguish between valid flow signals and transient EMI spikes.
- Use of Fiber Optic Communication
Instead of traditional wired signal transmission, some EMI-resistant flow meters use fiber optic cables, which are immune to electromagnetic interference.
EMI-Resistant Flow Meters: Electromagnetic Flow Meters (Magmeters)
- Magmeters use Faraday’s Law of Electromagnetic Induction to measure flow rate.
- Since they operate on induced voltage, they are naturally prone to EMI but can be shielded effectively.
- EMI-resistant Magmeters use noise-filtering techniques and shielded coils to ensure accurate readings.
Applications of EMI-Resistant Flow Meters
EMI-resistant flow meters are widely used in industries where electromagnetic interference is a concern.
- Oil and Gas Industry
Accurate measurement of crude oil, refined petroleum products, and natural gas in high-EMI environments with motors, pumps, and drilling equipment. - Power Plants
Measurement of cooling water, steam, and fuel flow in power generation facilities, where large generators and electrical systems create significant EMI. - Chemical and Pharmaceutical Industries
Precision dosing and flow control in chemical processing plants, where EMI from automated machinery can impact sensor performance. - Water and Wastewater Management
Reliable flow measurement in municipal water plants and industrial wastewater facilities, where electrical pumps and sensors operate in close proximity. - Food and Beverage Industry
Ensuring accurate measurement of liquids like milk, juice, and beer in processing plants with high levels of automation.
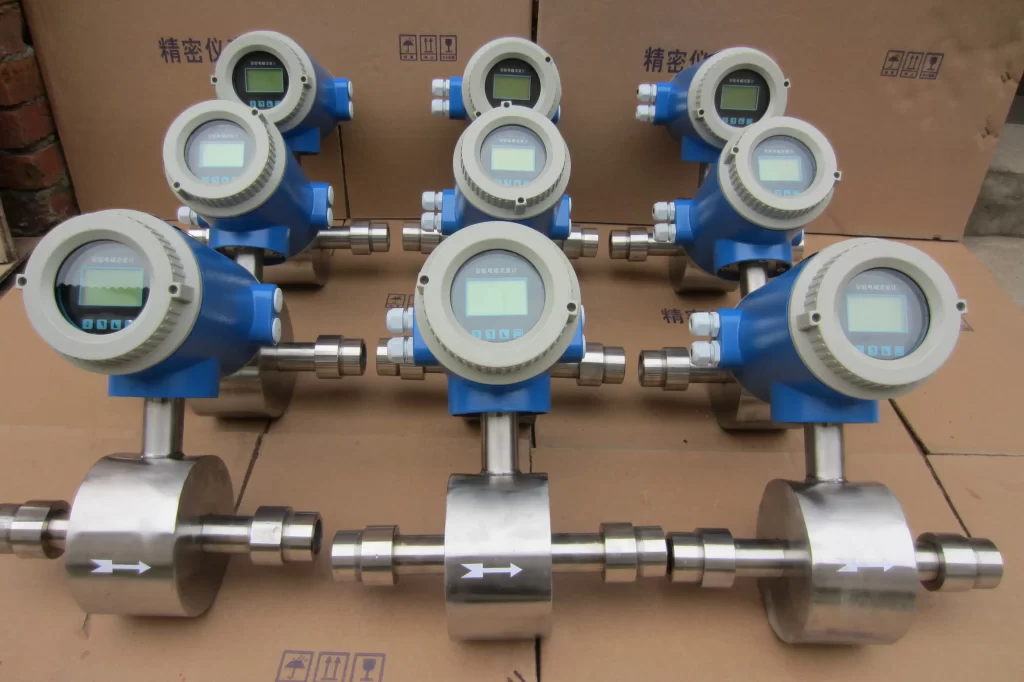
Application Cautions of EMI-Resistant Flow Meters
- Do not operate a magnetic flowmeter near its electrical conductivity limit. Because the flowmeter can turn off.
- Provide an allowance for changing composition and operating conditions. This can change the electrical conductivity of the liquid.
- In typical applications, magnetic flow meters are sized. So that the velocity at maximum flow is approximately 2-3 meters per second.
- Gravity fed pipes may require a larger magnetic flowmeter to reduce the pressure drop. So as to allow the required amount of liquid to pass through the magnetic flowmeter without backing up the piping system. Operating at the same flow rate in the larger flowmeter will result in a lower liquid velocity as compared to the smaller flowmeter.
- For slurry service, be sure to size magnetic flow meters to operate above the velocity at which solids settle (typically 1 ft/sec). To avoid filling the pipe with solids that can affect the measurement and potentially stop flow.
- Magnetic flow meters for abrasive service are usually sized to operate at low velocity (typically below 3 ft/sec) to reduce wear.
Why Does a Magnetic Flow Meter Need Grounding?
The electromagnetic flowmeter signal is weak, only 2.5~8mv at full scale. Only a few micro-volts when the flow rate is very small, and slight disturbance will affect the measurement accuracy.
So, the transmitter casing, shielded wire, measuring conduit and transmitter of the pipes. They must be grounded, and the grounding points should be set separately. They must not be connected to common ground lines such as motors and electrical appliances or to the upper and lower water pipes.
The converter part has been grounded through the cable, so do not ground again to avoid interference caused by different ground potentials.
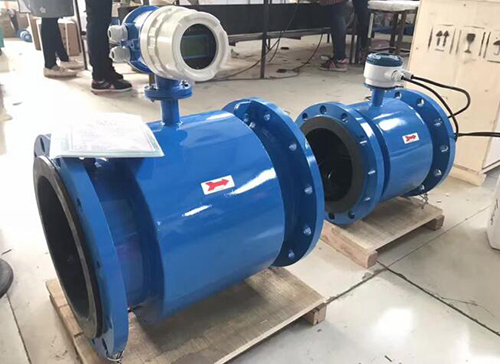
Installation and Maintenance Best Practices
To maximize the performance of EMI-resistant flow meters, proper installation and maintenance are essential. Here are some best practices:
- Proper Grounding and Shielding
- Ensure that the meter is properly grounded to prevent electrical noise from affecting the measurement.
- Use shielded cables to minimize conducted EMI.
- Optimized Sensor Placement
- Install flow meters away from high-EMI sources like VFDs, transformers, and large motors.
- Use physical barriers or EMI shielding materials if close proximity to EMI sources is unavoidable.
- Use of Surge Protectors and Filters
- Employ surge protectors to prevent sudden voltage spikes from damaging the meter.
- Use low-pass filters to block high-frequency noise from affecting signal transmission.
- Regular Calibration and Testing
- Periodically calibrate the flow meter to ensure continued accuracy.
- Conduct EMI testing in the operating environment to identify potential interference sources.
- Firmware and Software Updates
- Keep the meter’s firmware updated to benefit from the latest signal processing improvements.
- Use diagnostic tools to monitor EMI levels and optimize performance accordingly.
More Flow Measurement Solutions
- Helical Flow Meters: Accurate Flow Measurement For Challenging Applications
- Bitumen And Asphalt Level Meters: Let’s Learn More About Them
- Rotary Flow Meters for More Stable Measurement and Control Systems
- Fertilizer Flow Monitoring: Liquid Fertilizer Flow Meters
- Calorimetric Flow Meter: An Economical Solution For Hot Water Flow Measurement
- Knowing Paint Flow Meters – Choose the Right One!
- Comprehensive Guide On Chlorine Flow Meters
- How To Calculate Pressure From Flow Rate And Vice Versa
- Non-Contact Flow Meters: An Advanced Approach To Fluid Measurement
- Relationship Between Pressure And Flow Rate: Key Insights
Electromagnetic Interference Resistant Flow Meters stand for a significant leap forward in ensuring the reliability and accuracy of flow measurement in harsh conditions. By knowing the effects of EMI and harnessing advanced technologies, these flow meters provide unique resilience and performance. The importance of accurate flow measurement cannot be overstated, as it impacts product quality, operational efficiency, and safety across various industries.
As technological innovations continue to evolve, the future of EMI-resistant flow meters looks promising, with potential advancements in IoT, AI, and material science. These developments will further enhance the stability and reliability of industrial processes, making Electromagnetic Interference Resistant Flow Meters an indispensable tool in modern industry.
Sino-Inst’s flow meters have been serving in various industrial applications for a long time. EMI-resistant flow meters are an important part of our product catalog. Company’s Sales team is always at the service of customers, selecting suitable flow measurement solutions.