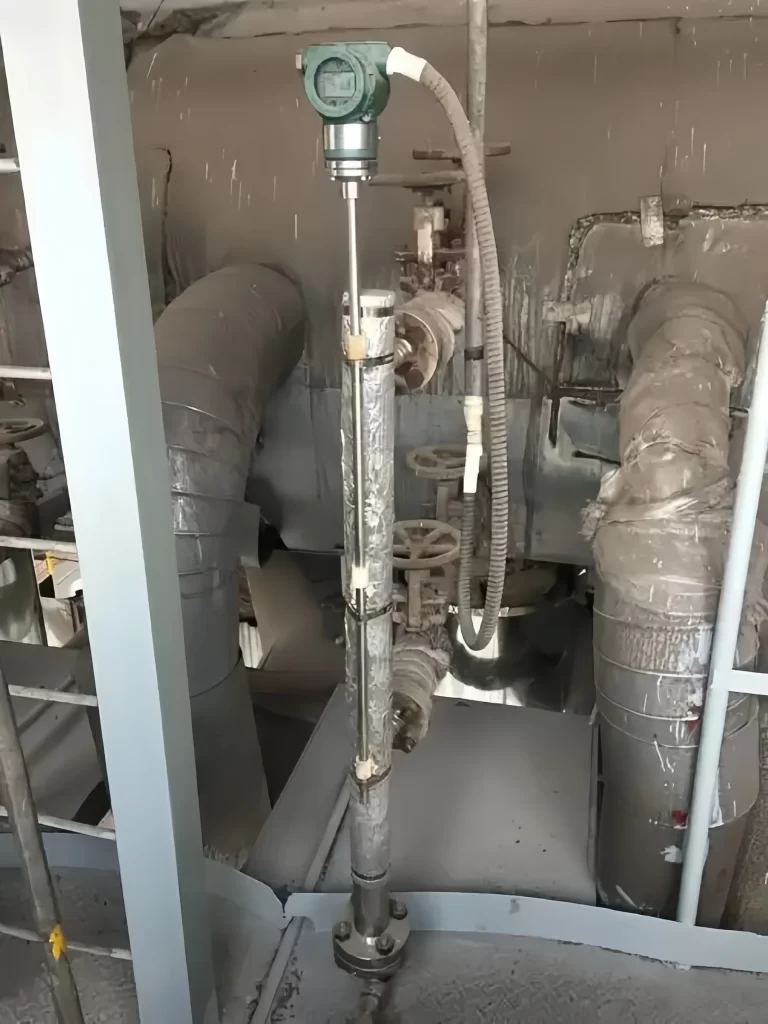
Level transmitters with a magnetic, high-resolution measuring principle are used for continuous level measurement of liquids and are based on determining the position of a magnetic float following the magnetostrictive principle.
This blog looks into each of the magnetic level instruments, their working principles, advantages, applications, comparability to other types of level measurement practical applications.
Magnetic Level Measurement
The magnetic Level Measurement process is triggered by a current impulse. This current produces a circular magnetic field along a wire made of magnetostrictive material, which is held under tension inside the sensor tube. At the point being measured (liquid level), there is a cylindrical float with permanent magnets acting as a position transducer, whose field lines run at right angles to the impulse magnetic field.
This magnetic field of the float tensions the wire. The superposition of these two magnetic fields triggers a mechanical wave in the wire. This is converted into an electrical signal at the end of the wire in the sensor housing by a piezoceramic pick-up.
Magnetic Level Measurement: Usages
Magnetic level measurement is commonly used in industries such as:
- Oil and gas
- Chemical processing
- Water and wastewater
- Power generation
- Food and beverage
The four most common devices used for magnetic level measurement are:
- Magnetic Level Indicator
- Magnetic Type Level Transmitter
- Magnetic Level Switch or Magnetic Level Sensor
Magnetic Level Indicator
A magnetic level indicator (MLI) is a visual gauge used to monitor liquid levels inside a vessel. It consists of a float that travels with the liquid surface and a magnetic coupling that moves an external indicator, usually a series of rotating flaps or a bar graph.
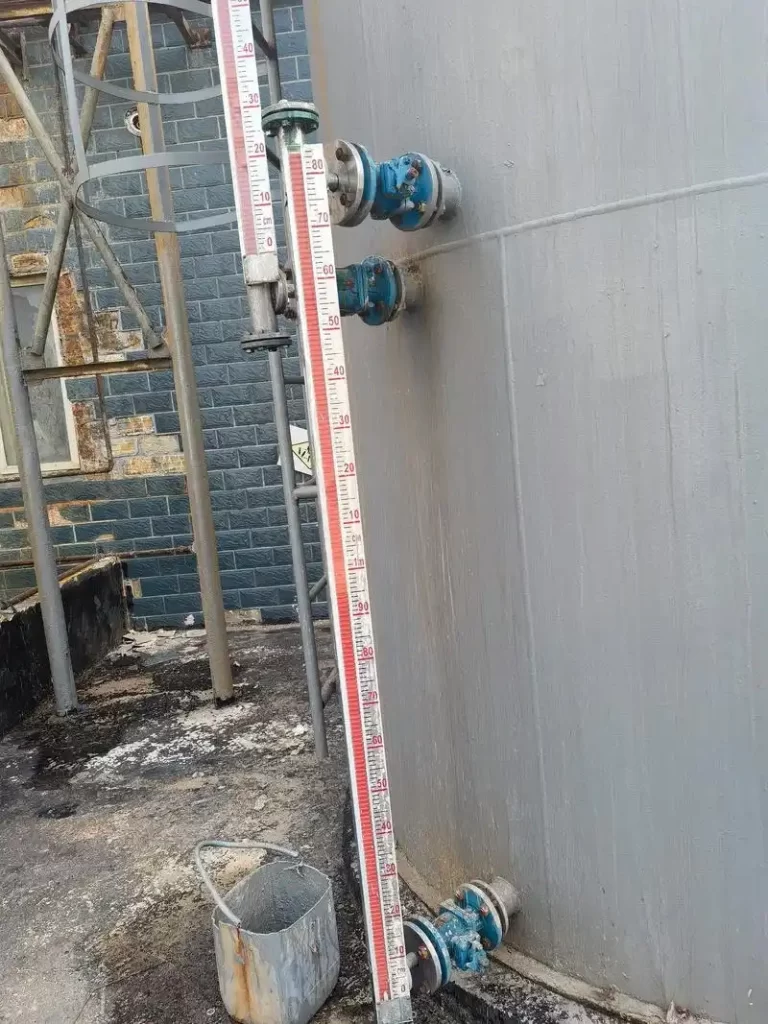
A float containing a strong magnet moves up and down as the liquid level changes. Outside the chamber, a series of magnetic flaps or rollers are mounted. As the float moves, the magnetic field causes the flaps to rotate and change color representing the liquid level visually.
Benefits:
- Clear, real-time visual indication
- No external power required
- Suitable for high-pressure and high-temperature applications
- Isolated from process fluid – reduces corrosion and maintenance.
Applications include Storage tanks, Pressurized vessels, and Aggressive or toxic liquids. Limitations such that it only provides local indication (unless combined with a transmitter), less effective for low-density or highly viscous fluids.
Magnetic Level Transmitter
With a magnetic level transmitter, process-and procedure-specific solutions are possible. These transmitters are frequently affixed alongside a magnetic level indicator to provide both visual and remote level monitoring.
It’s operating temperature: T = -90 … +450 °C [-130 … +842 °F];
Operating pressure: P = vacuum to 100 bar [1,450.4 psi];
Limit density: ρ ≥ 400 kg/m3 [25.0 lbs/ft3] and Resolution is < 0.1 mm.
Types of Magnetic Level Transmitters:
- Reed Chain Transmitter – Uses a chain of reed switches and resistors triggered by a moving magnet.
- Hall Effect Transmitter – Employs Hall effect sensors to detect the float’s position.
- Magnetostrictive Transmitter – Provides highly accurate level measurement using the time-of-flight principle for a torsional wave in a wire.
Benefits:
- Accurate and reliable
- Suitable for continuous level measurement
- Can integrate with PLCs, SCADA, and DCS systems
- Provides both local and remote monitoring
Applications include Refinery tanks, Chemical process vessels, High-pressure boilers, and Food-grade applications.
Certain Considerations are required. It requires a power supply. Installation may require calibration. Sensor types must be selected based on the application environment.
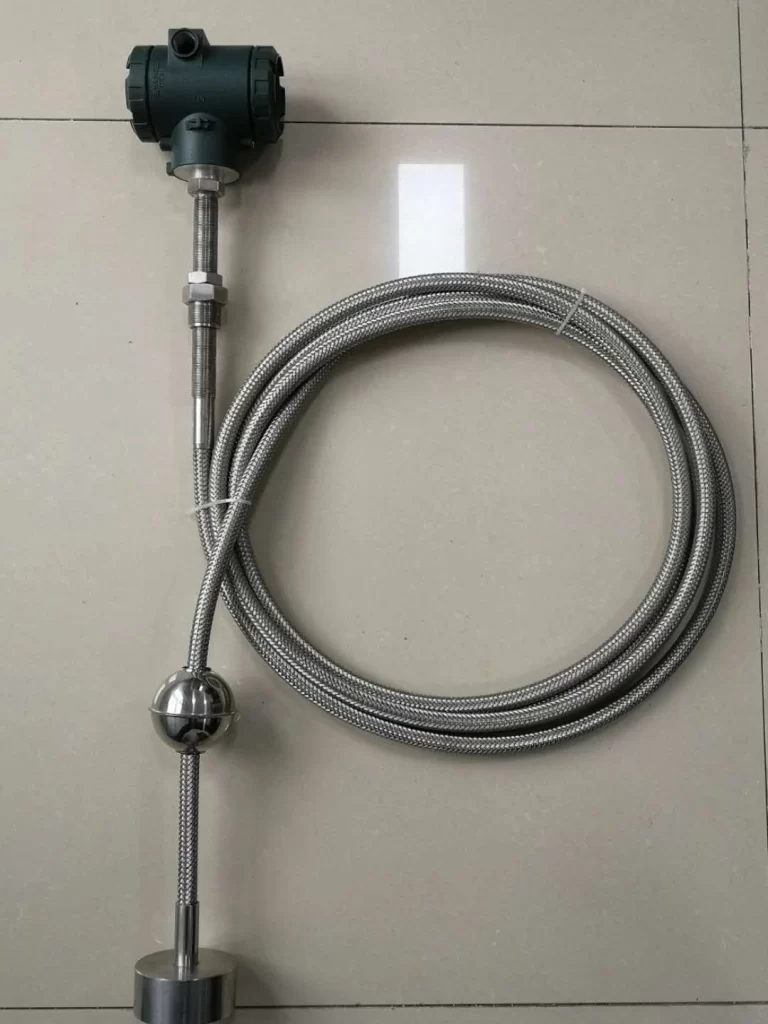
Magnetic Level Switch or Sensor
A magnetic level switch is a point-level sensing device that triggers an alarm when the liquid reaches a set level. These sensors are typically float-based, with magnets embedded in the float that activate a reed switch, proximity sensor, or relay.
Kinds of Magnetic Level Switch or Sensor
- Top-mounted magnetic level switch
- Side-mounted magnetic level switch
- Multi-point level switches (detect multiple levels within one unit)
When the liquid level reaches the float, the float moves and causes a magnetic field to activate the internal switch. The switch then sends a signal to the control system or directly to an actuator, pump, or alarm.
Benefits:
- Simple and cost-effective
- No external power needed (for reed-type switches)
- Reliable operation in harsh environments
- Easy to install and maintain
Applications include Overflow protection in tanks, Pump protection (low-level cut-off), High/low level alarms, and Interface level detection (e.g., oil-water separation).
Limitations are that they are only suitable for point-level detection. Not ideal for continuous monitoring.
Selection Criteria while Choosing a Magnetic Level Device
More Level Measurement Solutions
- GWR Type Level Transmitter: An All-inclusive Guide
- Single Point – Multi-Point Float Level Switches | Simple but Effective
- Different Solutions for Fluid Level Measurement
- Float Type Level Transmitters for Continuous Level Measurement
- All-inclusive Guide To Bin Level Measurement Systems
- An Out-and-Out Guide To Different Types Of Level Transmitters
- Tank Level Measurement with Pressure Transmitters/DP Transmitters
- Hydrostatic Level Measurement-Liquid Level Measurement with Pressure Sensors
With proper selection and maintenance, magnetic level measurement systems deliver long-lasting and accurate performance for years to come.
Through the above detailed discussion, you can speedily infer the working principles, benefits and limitations, and applicable scenarios of different types of Magnetic level measurement solutions.
We at Sino-Inst offer various types of Level transmitters. Including magnetic, radar, guided wave radar, hydrostatic pressure, ultrasonic, capacitive, float and other various measurement technologies. They are best suitable for level, interface and volume measurement for basic, challenging and extreme conditions in various industries.